In Corrèze, this SME with 120 employees has designed with its production operators a production monitoring and visual management system that is precise, ergonomic and in real time. The key: time, quality and productivity gains!
Since its creation in 1991, Tiag Industries has established itself as one of the European leaders in the production of technical plastic parts in medium series. For customers located all over the world (40% of turnover is achieved through export), and in all sectors: office or hospital furniture, packaging, construction, agricultural or construction machinery, weapons, etc. However, all these clients have one thing in common: high standards in terms of quality and responsiveness.
Competitiveness, flexibility, autonomy: the challenges of 4.0 at TIAG
To respond to this, this family-run SME (120 employees), whose 3 production units are in Corrèze, has therefore embarked on the gradual deployment of a 4.0 factory, based on Pingflow’s visual management solutions.
The objectives of this project?
- Simplify and make production monitoring more efficient;
- Minimize (or even eliminate) the risk of human error and therefore increase the level of production quality;
- All while giving back autonomy to the teams (operators, supervisors, shipping, administration, etc.) to allow them to focus on the really important tasks.
Production monitoring: the need for real-time information
Within the production units, monitoring was previously done “in the old fashioned way, on sheets of carbon paper”, says Christophe Laurent, the director of the factory. Simple… but not very effective!
“This system prevented us from having a precise vision at the moment T of the pace: to know where we were, we had to go over the machines”, laments Christophe Laurent. The configuration, exhausting for the team leaders who had to travel miles through the factory to follow the progress of production, was also stressful for everyone: “The search for information creates uncertainty, it puts production in danger and the employees in a situation of fatigue, therefore increases the risk of error”, notes Alexandre Moraine, CEO of the company.
Operational excellence: go faster, minimize non-conformities
Increasing the level of quality of operations was indeed the second expected benefit of digitizing the factory. Among the indicators to improve:
- the scrap rate (non-compliant parts),
- the downtime of the machines that must be re-configured between two series,
- incident resolution time
- the deadline for “picking up” the parts produced by the forklift drivers
Taken together, all these optimizations should improve TIAG’s productivity: “It’s about gaining in competitiveness compared to competitors in Eastern Europe in particular,” explains Alexandre Moraine. It is absolutely essential when we have made the choice of 100% made in France”.
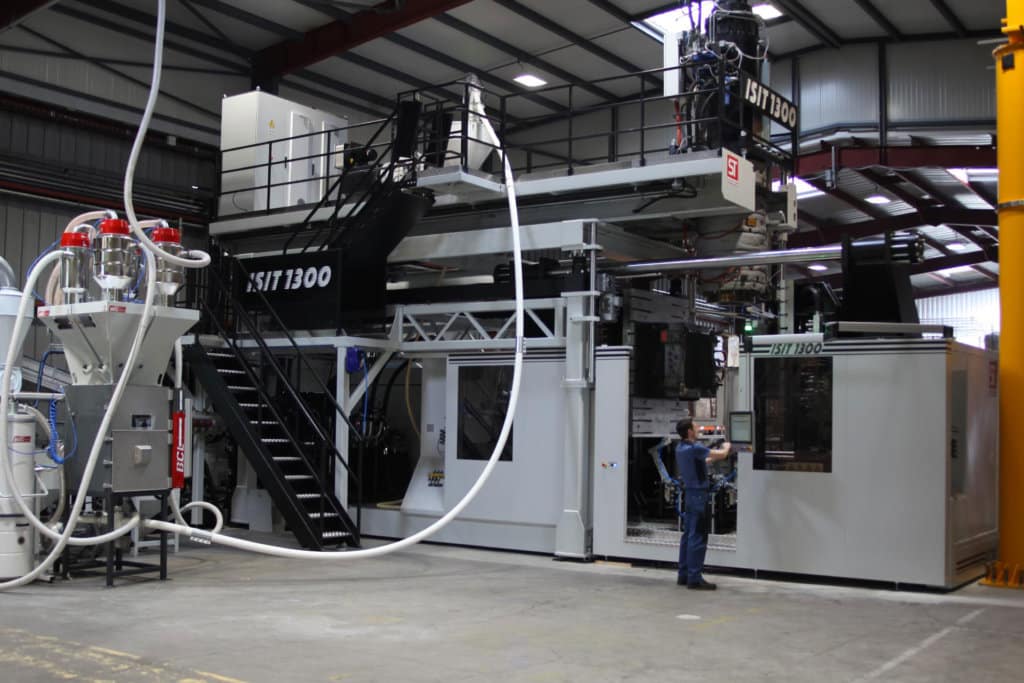
Digitization of production at TIAG Industries: progress step by step
In its 3 production units, TIAG implements several distinct industrial processes:
- injection,
- blow molding
- rotational molding
- assembly and finishing
Different machines, different teams and processes: it was neither possible nor desirable to digitize all the units at once. From 2020 to 2023, thanks to the permanent support of the Pingflow teams, a gradual deployment has therefore taken place.
2020-2021: a POC to experiment… and reassure
If Pingflow places the POC (proof of concept, i.e. a test in real conditions, but on a small scale) at the heart of its support process, it is for a good reason. And even several:
- technically, and in terms of business, each industrial context is different: to be efficient, a digital visual management solution must be perfectly adapted to the machine, and to the management requirements,
- in terms of IS, a solution like that of Pingflow connects to an existing system (often an ERP), with which it is necessary to be able to create a “dialogue”,
- the change induced is not only technical… far from it, even! A digital transformation is above all a human transformation: obtaining support (and valuable feedback) on the implementation of this new tool is a key benefit for this POC phase.
For this first stage, efforts focused on the operator console, a kind of tablet allowing people to declare and “monitor” their activity on their workstation.
![]() |
![]() |
The challenge, underlines Christophe Laurent, was to demonstrate to team leaders and operators how Pingflow was going to make their work easier, reassure them about the reliability of the tool… But also listen to and take into account their suggestions for improvement”. At the end of the POC, version 1 was therefore significantly improved:
- in terms of user interface (place, size, color of alert buttons, access to different actions, etc.),
- in terms of information provided: the numbers and times of the end of work orders, for example, an indicator that “speaks” to operators and team leaders.
The result ? An ergonomic 4.0 console, adapted to the uses, providing essential information in time (number of parts produced, scrap, etc.), and above all the first solid brick of a more extensive deployment.
READ ALSO > The 4.0 panel at the service of the operator
2021-2022: an expanding deployment
Following this conclusive POC, the operator consoles were generalized on all 8 TIAG blow molders in 2021, then on the fleet of 7 injection machines at the beginning of 2022.
But this deployment does not “only” concern workstations. Facilitating the work of operators is only one of the levers for the digitization of a factory through visual management, which Pingflow has enriched by:
- the rationalization of the andon alert process: given by the operator from his desk, it results in the display of the incident on the workshop display panels, followed by a second “escalation”
- alert to a second manager if it remains unanswered,
- the extension of the functions of the desk at the call of the forklift drivers, to come and collect the pallets of produced parts,
- the installation of large summary screens for monitoring production KPIs and displaying incidents at different locations in the plant.
![]() |
![]() |
READ ALSO > Andon digital alert: for a reactive and agile organization
Throughout the project: enrichments and agility
One of the keys to this successful deployment? The adaptability of the Pingflow teams… and of the tool itself, “in which it is very easy to add or remove elements, applications, which has greatly facilitated the work of optimizing the interfaces: we wanted it to be as easy to use as a smartphone,” appreciates Christophe Laurent.
And for everything that needed to be configured upstream, the Pingflow project teams were the driving force. Thus for the connection between Pingflow and the TIAG ERP, an essential ingredient of success for:
- follow the state of stocks,
- keep up-to-date information on maintenance, quality, start-up of new productions, etc.,
- all in real time, in order to facilitate information feedback internally, but also on the management and even customer side.
The results: more (and better) productive workshops
Increased responsiveness at all levels
Thanks to the system set up with the help of Pingflow, all the information relating to TIAG’s production is digitized, and therefore available in real time. This translates into significant time savings, at all levels of the company.
On the production side, first:
- the workshop managers and operator managers, since they only need to travel when an incident requiring their intervention has been proven, have “saved” between 5 and 8% of their working time,
- the operators themselves, relieved of the tasks of clocking in, counting, calling the forklift drivers, etc. have saved considerable time on their daily tasks,
- finally, the plant management fully benefits from a super-smooth transfer of information. “It’s simple, rejoices Christophe Laurent: today I know exactly, and in a handful of seconds, where we are in the workshop!”
This streamlining of production monitoring also has beneficial impacts far beyond production stations:
- in logistics, with better optimization of driver rounds thanks to the call function integrated into operator consoles,
- upstream and downstream, with more than 2 working days saved at the administration level: all entries are now automated, allowing these teams to focus on other tasks.
Increased quality and compliance
The other great advantage of digitization is to minimize (or even eliminate) the risk of human error. At TIAG, this means:
- on the administration side, by a considerable reduction in order entry errors and the monitoring of daily production results, thanks to the automation and reduction of tasks,
- on the production side, by a drop in the scrap rate (non-compliant parts) to 0.8%.
Incidents under control
The third major benefit is a “classic” of factory digitalization projects led by Pingflow: from reporting to resolution, incident management is fully optimized thanks to an andon digital alert system integrated into all operator consoles. Previously, locating a problem on the machine park could take up to 30 minutes… Time reduced to a minimum today.
Consequences?
- Operators gain in serenity and comfort, since they have the certainty that their alert will be seen and processed quickly,
- Their supervisors better prioritize their priorities and their time between setting up machines, training an operator, urgent tasks and important ones…
In short, it’s unanimous: “Today, all users tell me: there’s no going back, the new system makes their job much easier! », concludes Christophe Laurent.
READ ALSO > Andon system: CLAAS digitize its incident’s management
Projects full of boxes
The balance sheet? It is therefore more than satisfactory. “A few years ago, I took lessons by visiting our customers’ factories. Today, they are surprised at the level of digitization and efficiency we have achieved!”, appreciates Alexandre Moraine.
But this is a provisional assessment, because these first successes gave ideas to the TIAG Industries teams! The next areas for improvement identified?
- Optimization of production processes: “using all our individual data points (incidents, delays, small load breaks, etc.) we intend to identify where recurring blockages occur, and better prevent them”, points out Christophe Laurent.
- Traceability and communication with customers, by allowing operators and team leaders to “feed” the system set up with Pingflow: identification of batches in production, sending commented photos of parts, etc.
- Management and business strategy. “The idea is to use the data collected more systematically thanks to Pingflow and our ERP for AIC, but also for meetings focused on productivity leads”, imagines Alexandre Moraine.
“Thanks to Pingflow, we are fortunate to have a tool that communicates objective, indisputable information to us: it’s up to us to seize it,” concludes the manager.