Système Andon
Optimisez la réactivité de vos équipes
Le système Andon accélère la détection et la résolution des incidents, en plaçant les opérateurs au cœur de la qualité, de la sécurité, et de l’excellence opérationnelle. Outil clé du lean manufacturing, il se digitalise pour une réactivité optimale.
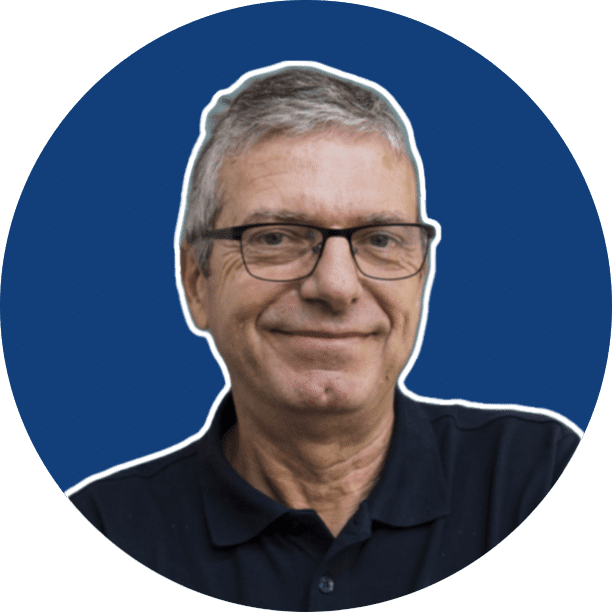
Echanger avec notre expert !
Divisez vos temps d’arrêt par 2 et plus
Détectez les incidents et accélérez vos interventions grâce aux alertes en temps réel !
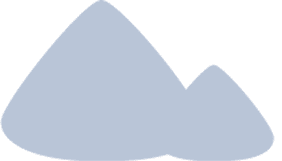
+5% à +15% de performance !
Analysez les interruptions, ajustez vos processus et optimisez votre TRS pour gagner en performance !
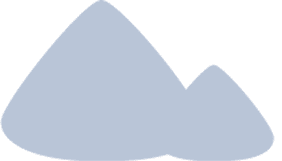
Améliorez en continu
Exploitez l’historique des alertes, identifiez les causes récurrentes et anticipez les problèmes !
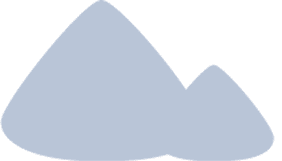
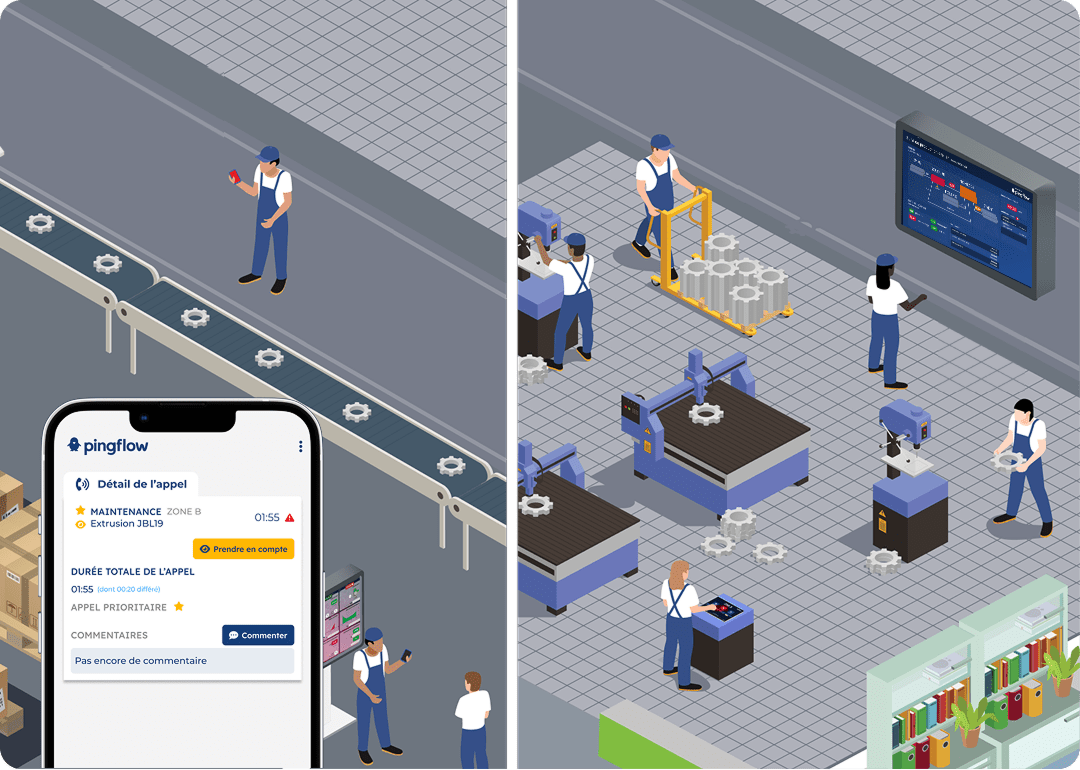
1. Appel andon
L'opérateur signale un problème sur la ligne de production grâce à l'application mobile.
2. Restitution atelier
À l'autre bout de l'atelier, la manager consulte le problème en direct sur grand écran.
Comprendre le système Andon
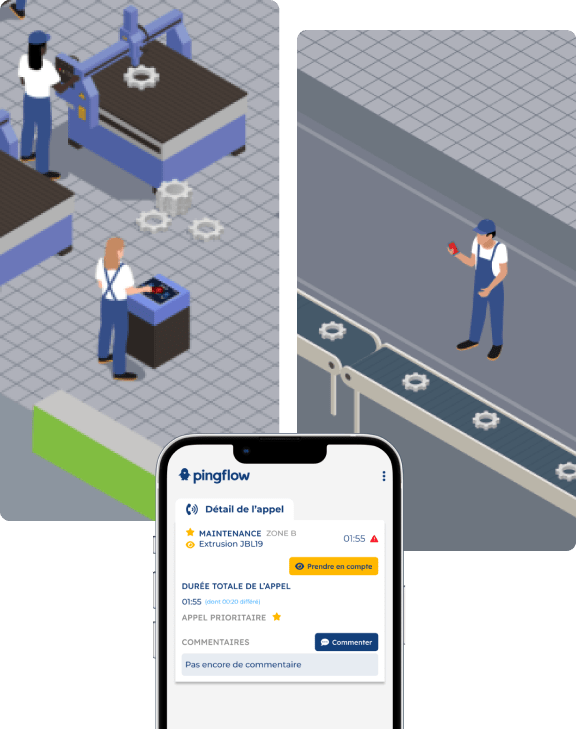
L’andon opérateur
L’opérateur déclenche une alerte depuis son poste de travail pour signaler un incident. Cela peut concerner une panne, un arrêt de production, un défaut qualité ou un besoin d’assistance.
Ce type d’Andon est particulièrement utile pour impliquer les équipes terrain dans l’amélioration continue et favoriser la réactivité des encadrants.

l’Andon machine
Les machines sont équipées de capteurs et systèmes de monitoring permettant de détecter automatiquement les anomalies (pannes, baisses de performance).
L’alerte est transmise immédiatement aux équipes de maintenance pour une intervention proactive et une réduction des arrêts de production.
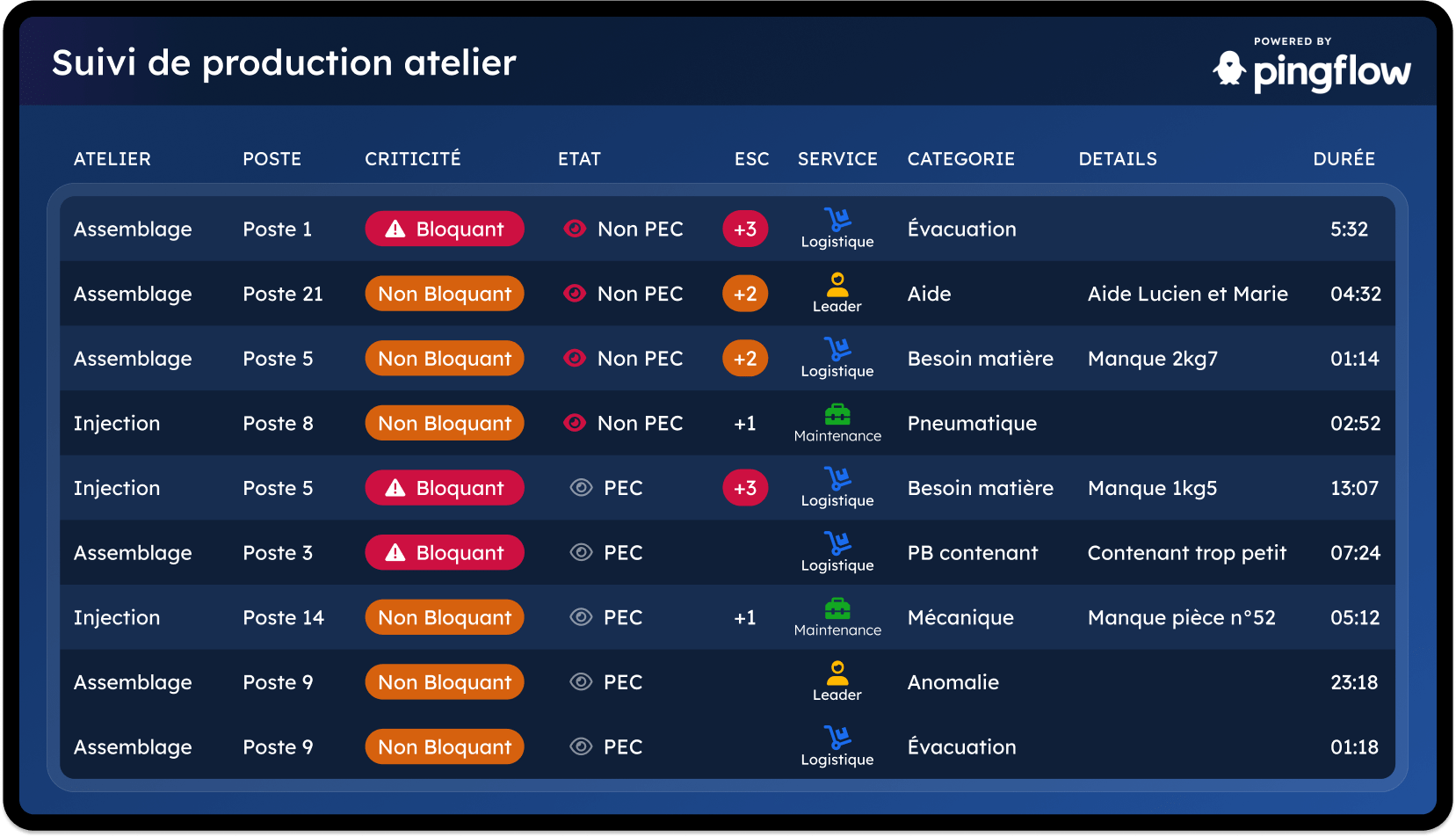
l’andon qualité
Il est utilisé pour identifier et signaler les dérives de qualité en temps réel. Lorsqu’un problème est détecté, une alerte est envoyée au service qualité pour un contrôle immédiat.
Cela permet de réduire le coût de la non-qualité en évitant la production de lots défectueux.
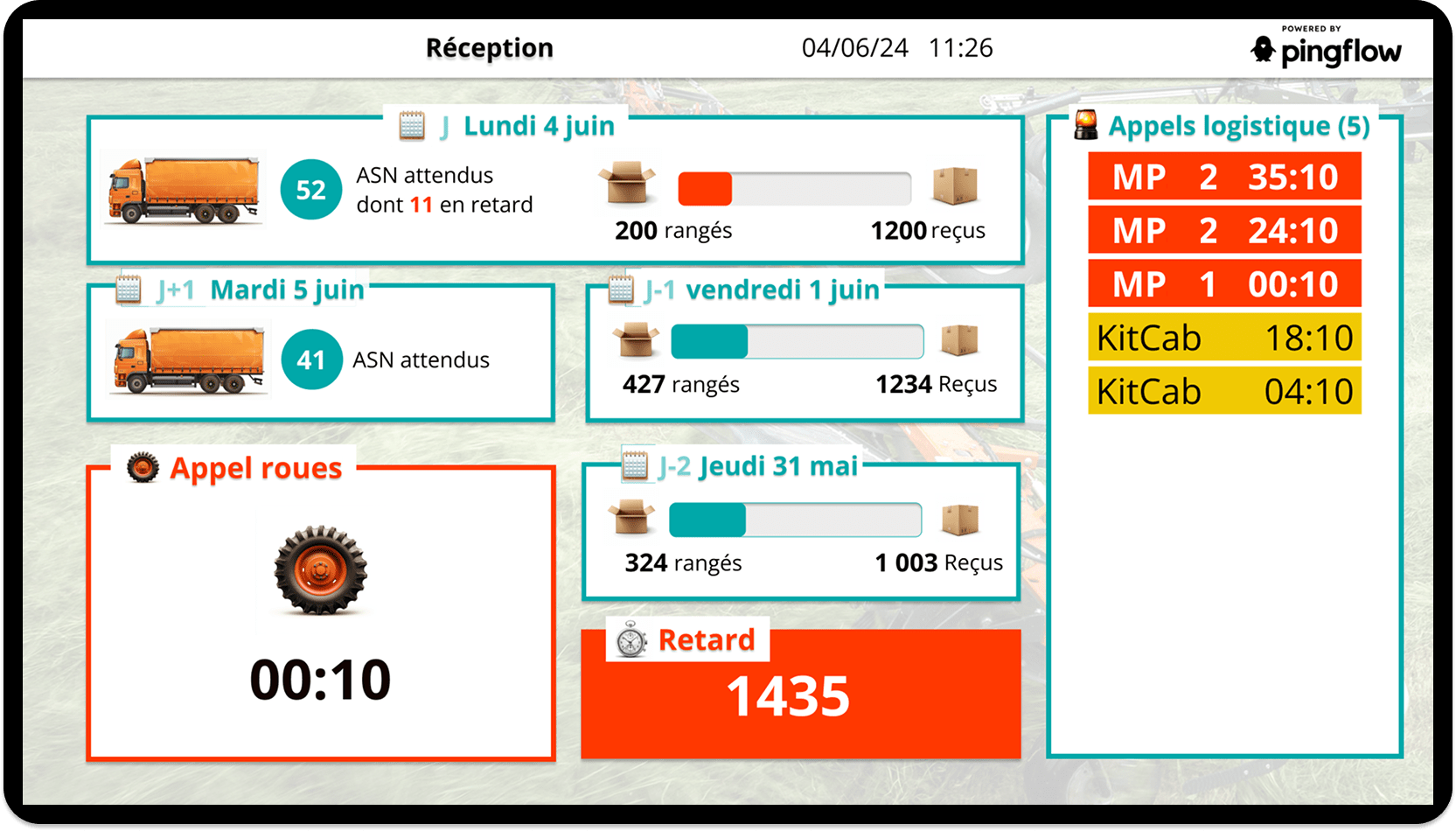
l’Andon logistique
Il permet d’optimiser les flux logistiques en déclenchant une demande de réapprovisionnement dès qu’un stock atteint un niveau critique.
L’alerte est envoyée aux caristes ou responsables logistiques, garantissant un réassort fluide et sans rupture.
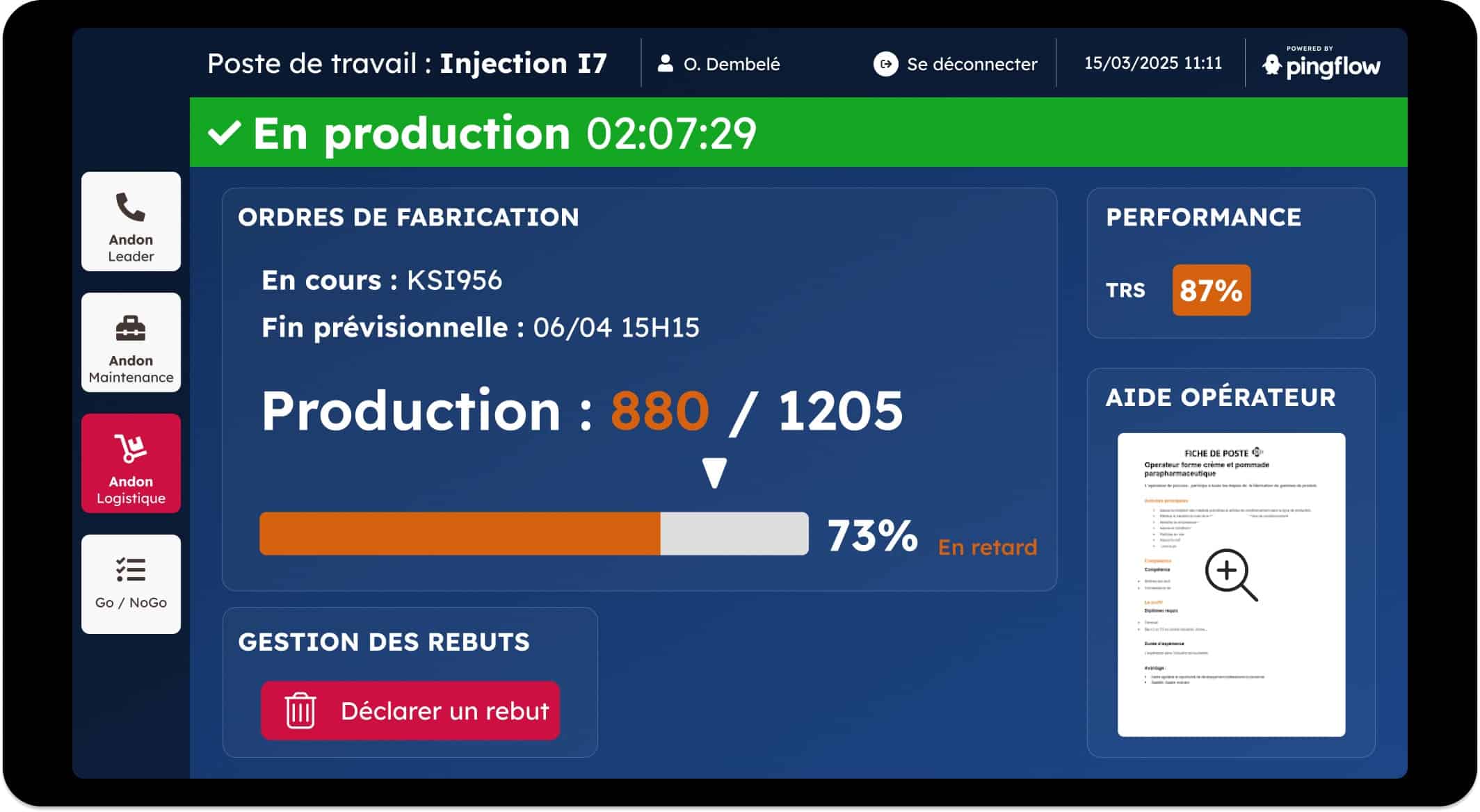
La production actuelle est de 880 pièces sur 1205, soit 73% de l'objectif atteint, avec un indicateur « En retard ».
Sur le côté droit, des indicateurs affichent une performance TRS de 87% et un encart d'aide opérateur.
Sur la gauche, quatre boutons sont visibles : Andon Leader, Andon Maintenance, Andon Logistique et Go/NoGo.
En bas, un bouton rouge permet de déclarer un rebut."/>
l’andon kpi
Il est utilisé pour suivre l’avancement de la production en temps réel et détecter les écarts par rapport aux objectifs (Takt Time, cadence, retards).
Il offre aux managers et aux équipes une vision claire de la performance et permet d’ajuster les ressources en conséquence.
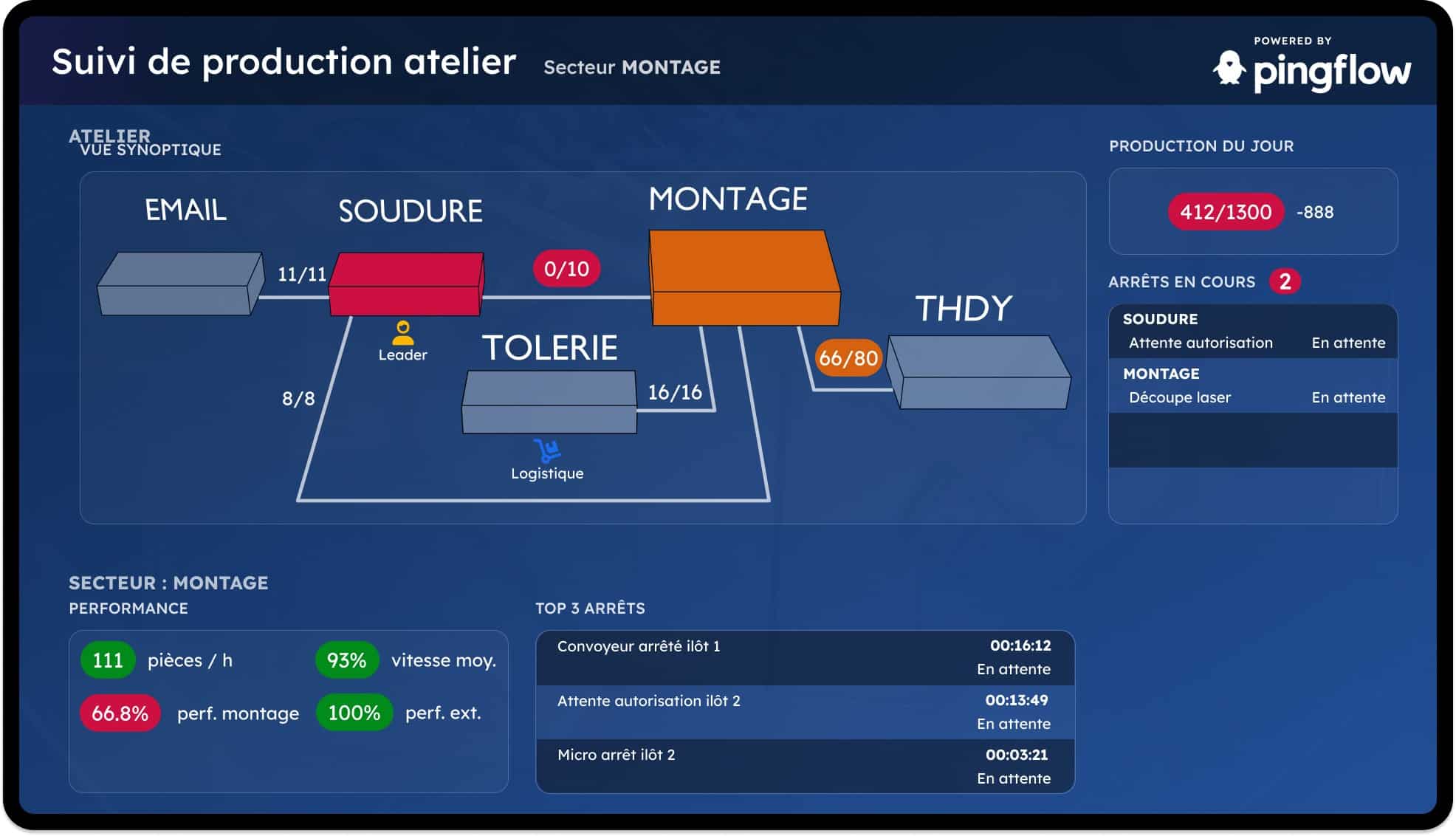
L’andon pilotage
Il est connecté aux systèmes d’information (MES, ERP, IoT), cet Andon synchronise production, qualité et logistique pour une prise de décision optimisée.
Il permet d’assurer une gestion agile et automatisée des alertes et des priorités.
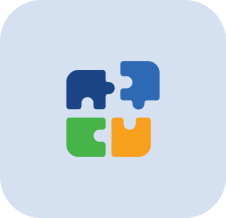
Gagnez en réactivité et en performance
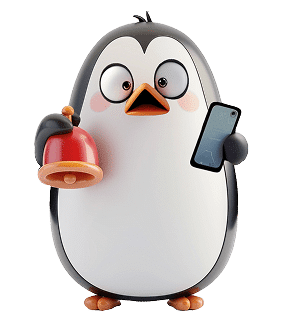
Détection
L’opérateur ou la machine signale un problème (panne, qualité, approvisionnement) via un bouton, une tablette ou un capteur connecté.
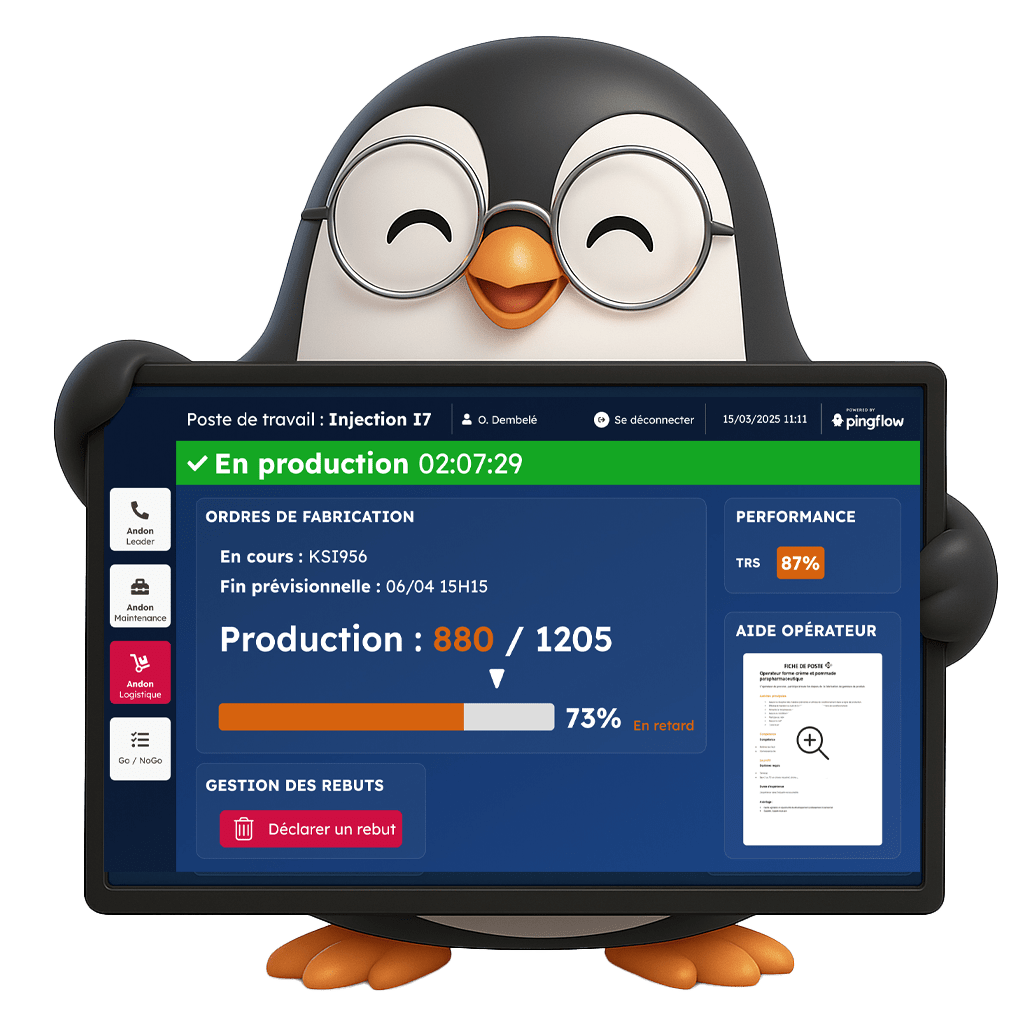
Signalement
L’alerte est envoyée en temps réel aux équipes concernées via des écrans, notifications mobiles ou e-mails pour une prise en charge immédiate.
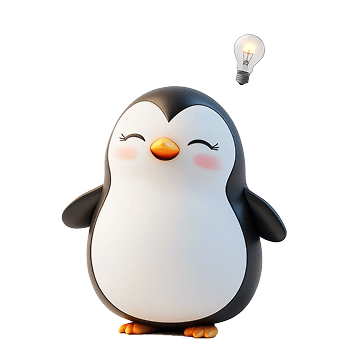
Intervention
Une fois l’alerte reçue, l’équipe concernée intervient directement sur le terrain pour diagnostiquer et résoudre le problème.
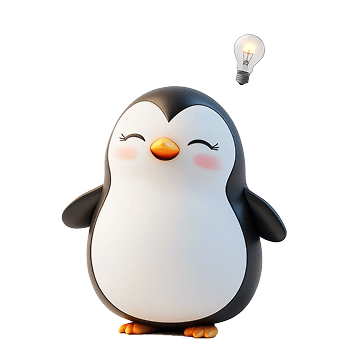
Suivi & amélioration continue
Chaque alerte est historisée et analysée afin d’identifier les tendances, les causes récurrentes et les axes d’amélioration possibles.
Application mobile : vos alertes à portée de main
Recevez et traitez vos alertes Andon en temps réel directement depuis votre mobile. Visualisez, suivez et mettez à jour les incidents en un clin d’œil grâce à une interface simple et intuitive.
Réagissez plus vite, suivez l’évolution des interventions et assurez une gestion fluide des alertes, où que vous soyez. Optimisez votre réactivité et améliorez la performance de votre production !
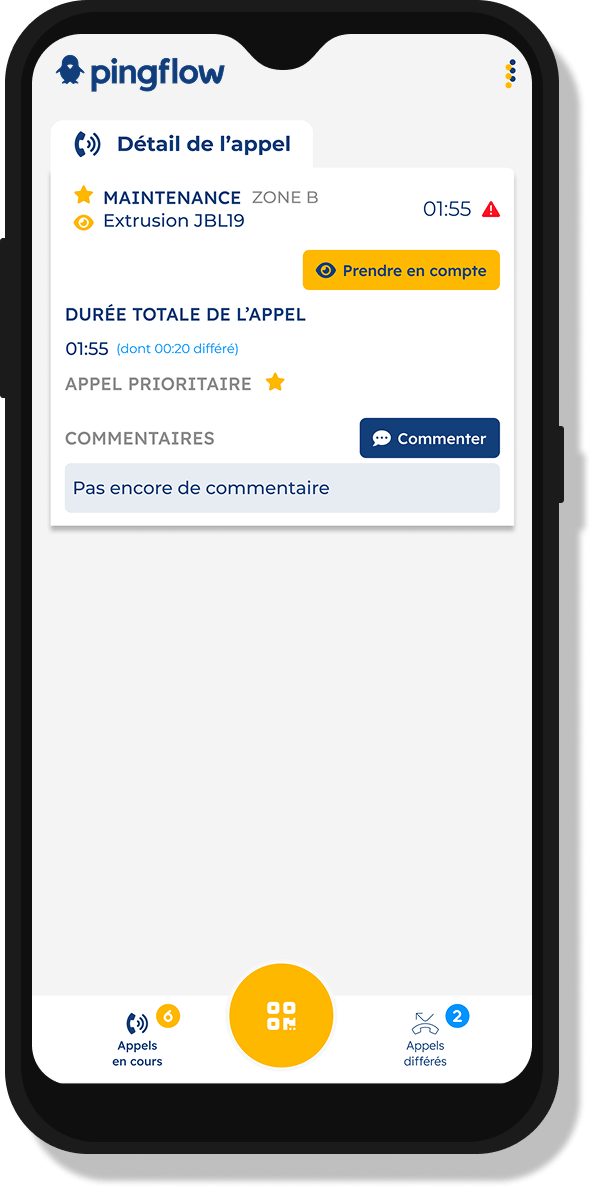
Ils ont optimisé
leur flux de production
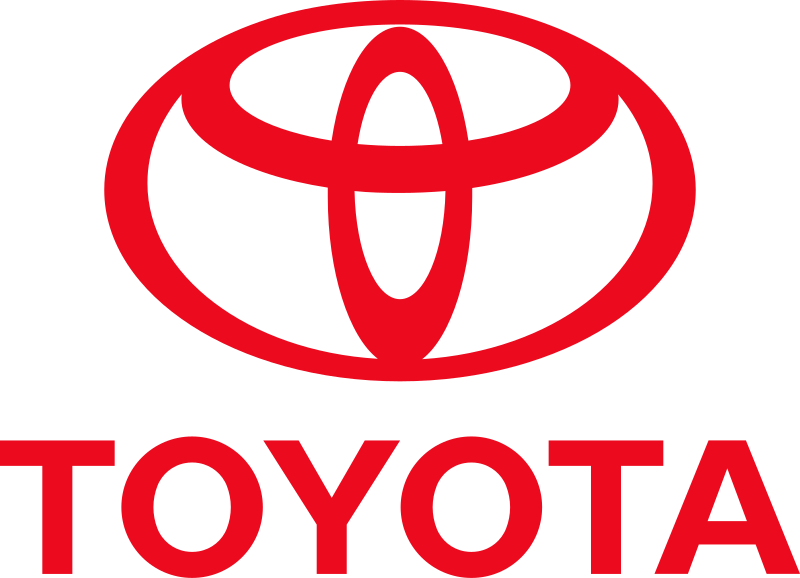
Ingénieur de Production
“Chaque projet mené avec Pingflow renforce nos process, booste notre productivité et met nos opérations sous contrôle.”
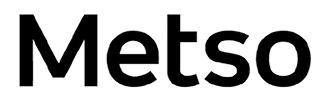
Directeur de site
« Avec Pingflow, on a gagné en productivité et en engagement. Les infos sont claires, fiables, et disponibles en temps réel. »
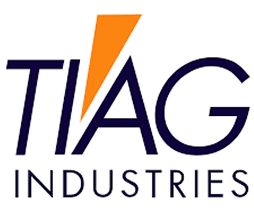
Directeur de site
“Grâce à Pingflow, nos équipes sont plus réactives et autonomes, avec une visibilité instantanée sur les alertes.”
Ils en parlent mieux que nous…
Une solution intuitive et modulable, conçue pour répondre à vos besoins d’autonomie et d’efficacité dans la gestion de la production.
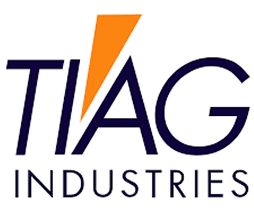
Directeur de site
“Grâce à Pingflow, nos équipes sont plus réactives et autonomes, avec une visibilité instantanée sur les alertes.”
Quelques wallboards Andon
Les wallboards sont créés sur mesure en fonction de vos besoins.
Tout savoir en 5 minutes
Découvrez comment l’Andon peut transformer votre performance opérationnelle.
Études de cas, astuces concrètes et méthodes éprouvées vous attendent !
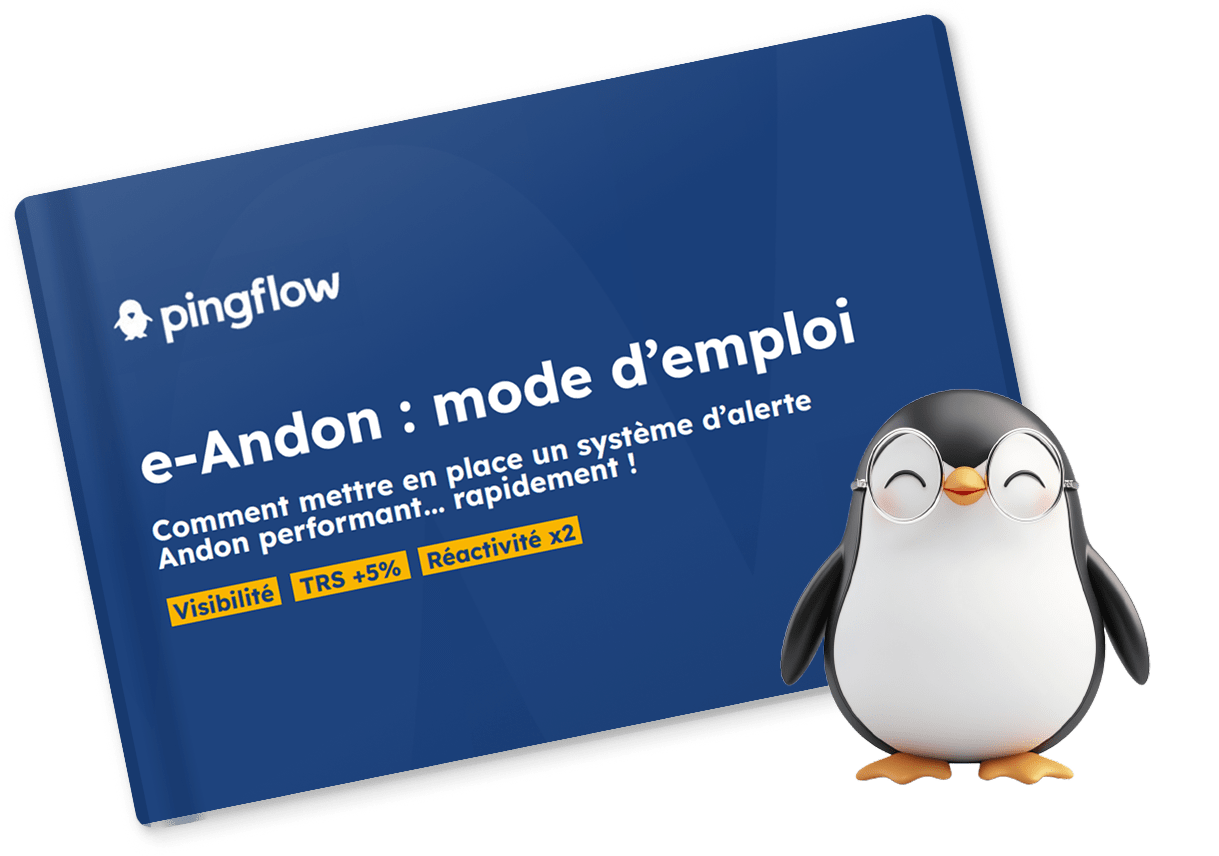
L’Andon… et au-delà 🚀
Découvrez comment cette fonctionnalité se combine avec d’autres usages !
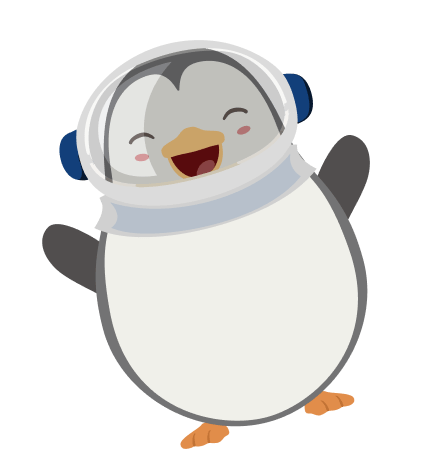
Tout frais de la banquise !
On vous envoie chaque mois une dose de contenus utiles et inspirants pour booster vos performances industrielles et logistiques.
Des cas clients, des outils pratiques, des tendances, et nos dernières nouveautés – sans blabla.
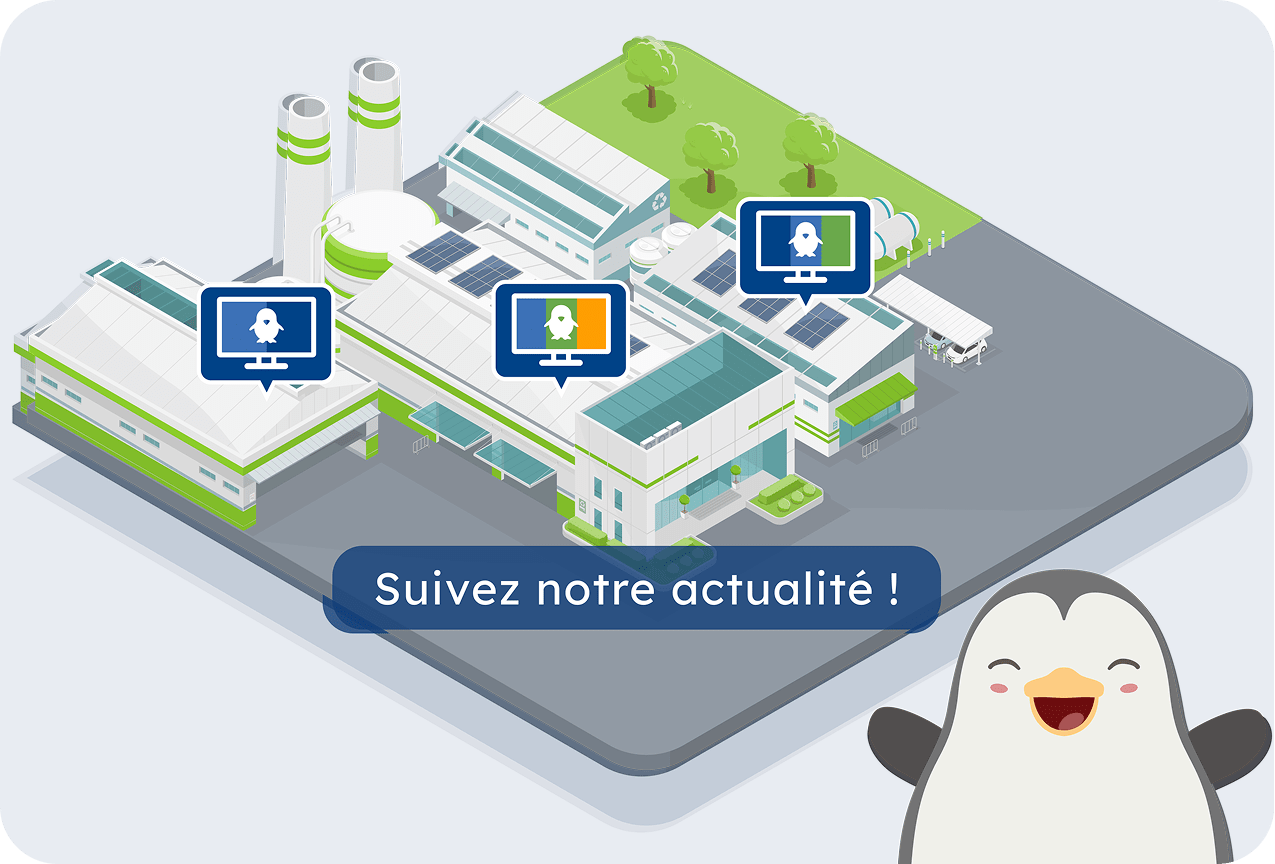
Pour aller plus loin…
Explorez nos articles pour approfondir votre compréhension du système Andon !
Découvrez des cas concrets et obtenez des conseils pratiques pour digitaliser votre site industriel.
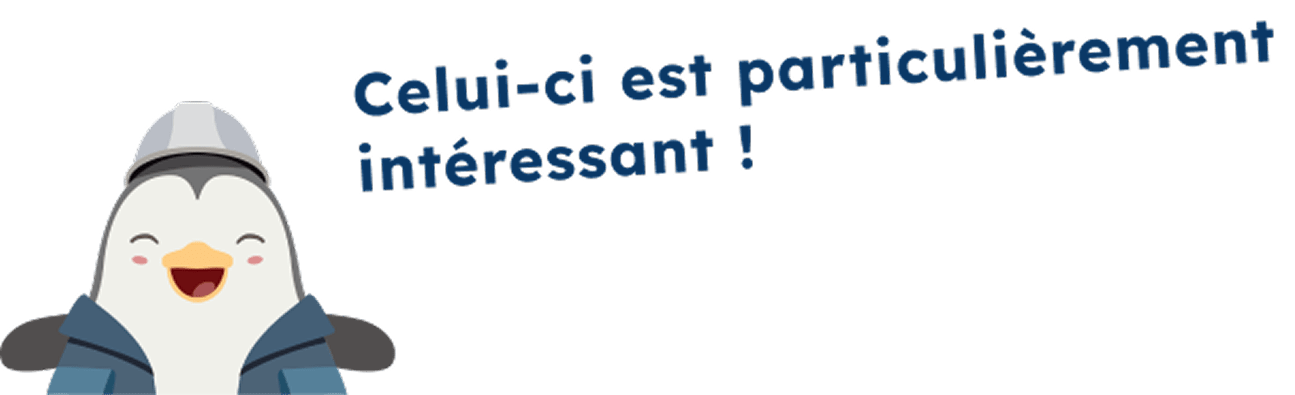