Pingflow a piloté la conception et l’installation d’un système Andon digital dans l’usine du Mans de CLAAS. Un système dont la flexibilité et la connectivité ont grandement aidé l’industriel dans sa démarche d’amélioration continue.
CLAAS, c’est une entreprise allemande fondée en 1913. Et l’un des leaders mondiaux dans le secteur des machines agricoles, avec 3,7 milliards d’euros de chiffre d’affaires en 2017, et plus de 10 000 salariés un peu partout dans le monde : Allemagne, Chine, Inde, Russie, USA… et France, où l’usine du Mans emploie 800 personnes (sur les 1000 salariés que compte CLAAS Tractor au total).
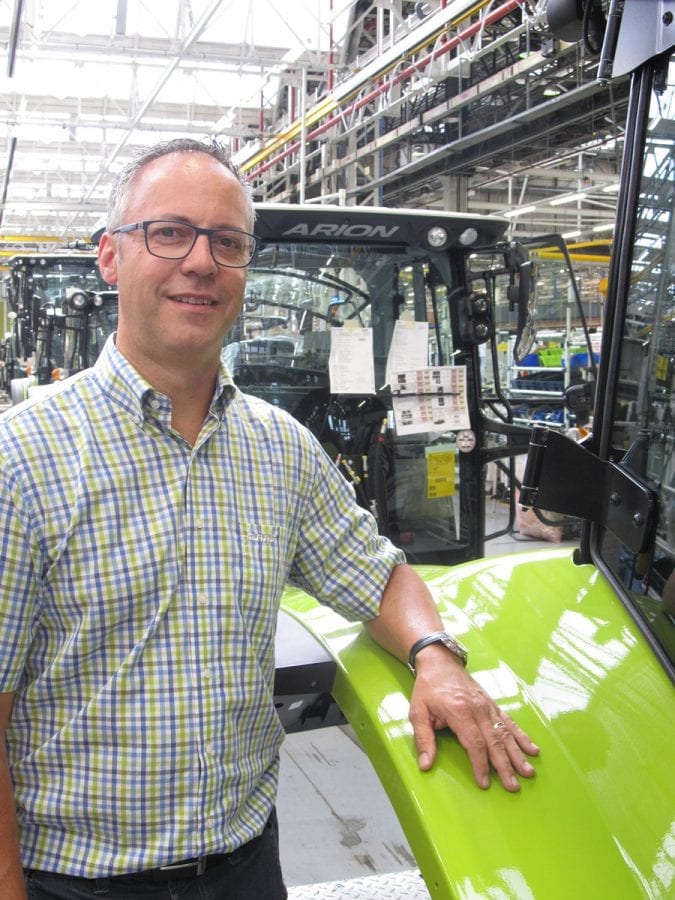
Au Mans, une seule ligne pour une multitude de tracteurs différents
Au Mans, plus de 10 000 tracteurs CLAAS des gammes, AXOS (de 75 à 100 chevaux), ARION (de 90 à 205 chevaux) et AXION (205-445 chevaux) sortent des lignes de production chaque année.
« Cela nous fait 2 grandes familles et 13 sous-types et 110 modèles de tracteurs, détaille Fabrice Porteboeuf, expert CXS (CLAAS Excellence System) de l’usine depuis 2003. Tous sont assemblés sur la même ligne, puisque nous fonctionnons en mix-production pour nous adapter aux commandes ».
La conséquence ? L’approvisionnement en pièces doit être ultra-flexible et réactif pour adapter la production au plus vite. Quant aux opérateurs, ils doivent avoir intégré, pour chaque modèle en production, le choix des pièces et le process associé.
L’Andon, une méthode éprouvée chez CLAAS
Tous ces impératifs expliquent aussi que CLAAS se soit intéressé très tôt à l’Andon. Depuis une dizaine d’années, ce système mis au point par Toyota et qui signifie « lumière où il faut aller» en japonais a été adopté à l’usine du Mans.
Au sens propre : le premier dispositif installé par Fabrice Porteboeuf et ses équipes consistait en de longues ficelles, reliées à des télérupteurs, stratégiquement placées sur les postes de travail. Et dès qu’un opérateur tirait pour signaler un problème, le numéro du poste s’allumait sur de grands tableaux lumineux situés sur la ligne d’assemblage.
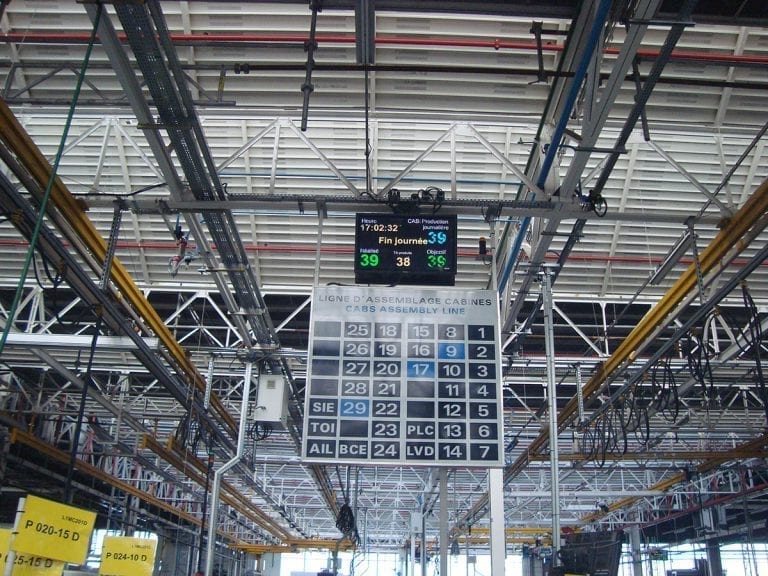
L’Andon première version : un système trop figé
Un système qui dans l’ensemble donnait satisfaction, mais souffrait de deux gros défauts. Le premier ? « Lorsqu’on tirait la ficelle, la lumière s’allumait, mais l’opérateur n’avait pas la certitude que son team leader avait pu la voir et allait intervenir : cela pouvait créer du stress », explique Fabrice Porteboeuf.
CLAAS a bien testé d’y ajouter un signal musical pour mieux signaler l’alerte. Mais entre les choix de jingle qui ne satisfaisaient pas tout le monde, et le niveau sonore qui dérangeait les opérateurs sans alerter efficacement les chefs d’équipes, l’essai n’a pas été concluant.
Deuxième tare, « c’était un système figé, déplore Fabrice Porteboeuf : les ficelles et numéros des postes sur les tableaux lumineux ne se modifient pas aisément. Or notre plan produit change en permanence, de nouvelles gammes et modèles sont apparus et ont donc modifié la répartition des postes de travail… Bref, c’était devenu inadapté ».
e-Andon : le premier vers l’usine 4.0
Découvrez les principes de fonctionnement de l’Andon, ses dernières innovations, les types d’opérations industrielles qu’il optimise, ainsi que son ROI pouvant atteindre +15 % de TRS et ses bénéfices concrets en production.
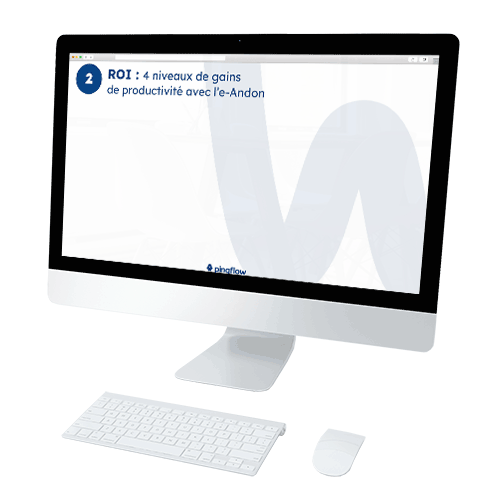
Le choix de l’Andon digital de Pingflow
En 2013, la décision a donc été prise de changer en profondeur le dispositif Andon de l’usine mancelle. « Pour nous accompagner, nous avons très rapidement choisi Pingflow, se souvient Fabrice Porteboeuf. D’abord parce que les interlocuteurs capables de comprendre nos problématiques spécifiques d’informatique industrielle et de téléphonie ne sont pas très nombreux sur le marché ».
Mais aussi parce que l’équipe Industrie 4.0 de Pingflow a su être force de proposition, accompagner CLAAS dès la rédaction d’un cahier des charges adapté aux besoins et contraintes de l’usine…
Et apporter une solution rapide (à peine 5 mois entre le premier contact et la mise en place du nouveau système Andon) autant qu’innovante. « Les boutons piézoélectriques radio qui commandent aujourd’hui le déclenchement des alertes Andon, par exemple, nous étaient totalement inconnus », reconnaît Fabrice Porteboeuf.
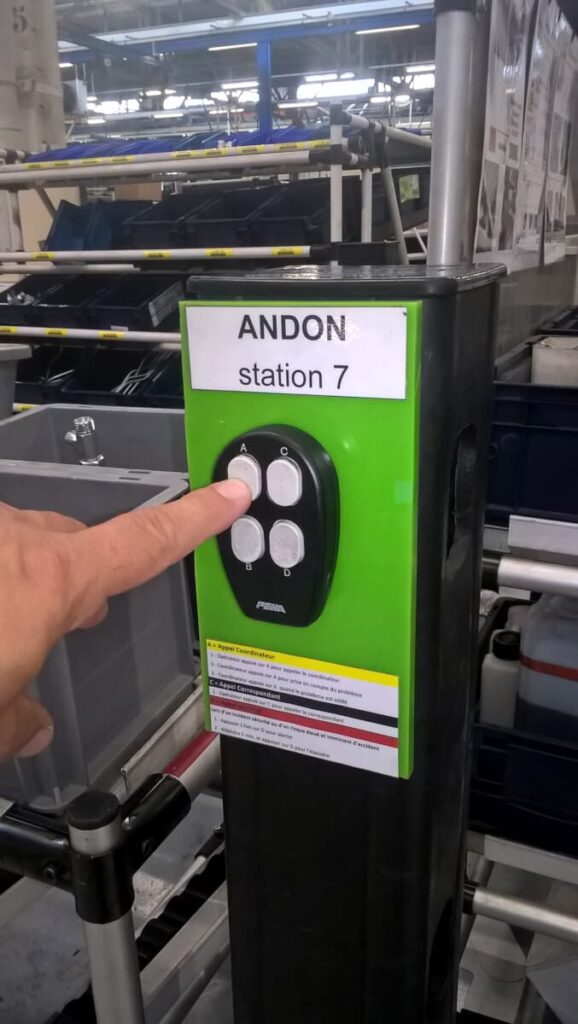
Le boîtier Andon digital : un gain de flexibilité
Or ces boutons changent radicalement la donne. D’abord parce qu’ils n’ont pas besoin d’être alimentés et qu’ils transmettent le signal d’alerte sans fil, et sur une simple pression. Ce qui signifie concrètement que les équipes de CLAAS peuvent les installer où bon leur semble, là où ils en ont besoin.
Ensuite parce chaque boîtier Andon fourni par Pingflow comporte non pas un, mais quatre boutons. Donc potentiellement 4 typologies d’alertes différentes. « C’est très utile pour nous, se félicite Fabrice Porteboeuf. Avec l’ancien système, impossible de faire la différence entre les différents cas de figure. Or savoir dès le signalement la nature du souci, c’est un gain de temps considérable ».
Chez CLAAS, les alertes catégorisées par le nouveau système Andon sont désormais de 3 types :
- Problème d’assemblage (une pièce montée trop serrée, ou trop juste) qui empêche l’opérateur de réaliser sa tâche
- Problème d’approvisionnement (pièce manquante)
- Problème de sécurité (incident sécurité, ou risque élevé et imminent d’accident, nécessitant l’intervention du chef d’équipe, de l’infirmier et du CHSCT)
L’alerte Andon digitale : plus de vitesse, moins de stress
Les bénéfices de la mise en place du système Andon conçu par Pingflow vont toutefois bien au-delà. C’est en effet tout le processus d’alerte qui a pu être revu.
Au lieu de l’ancien signal lumineux, le boîtier Andon déclenche désormais l’envoi d’un SMS vocal sur le téléphone du team leader et lance l’affichage du numéro du poste en alerte sur les écrans TV. Puis, un second s’il n’intervient pas. Et enfin une « escalade » vers son supérieur hiérarchique.
« Double avantage pour nous, apprécie Fabrice Porteboeuf : un, l’opérateur qui donne l’alerte est désormais certain qu’elle va être vue. Et deux, vue rapidement : nous avons gagné en moyenne 30 secondes de temps de réaction sur les alertes Andon ».
Comme le système Andon de Pingflow est connecté aux automatismes de CLAAS, il est capable de localiser les incidents, et ce en temps réel. L’action sur les incidents est donc plus rapide.
Et après l’incident, ce système permet l’édition de rapports de production plus facilement, plus utiles à l’animation des équipes et à la fiabilisation des processus.
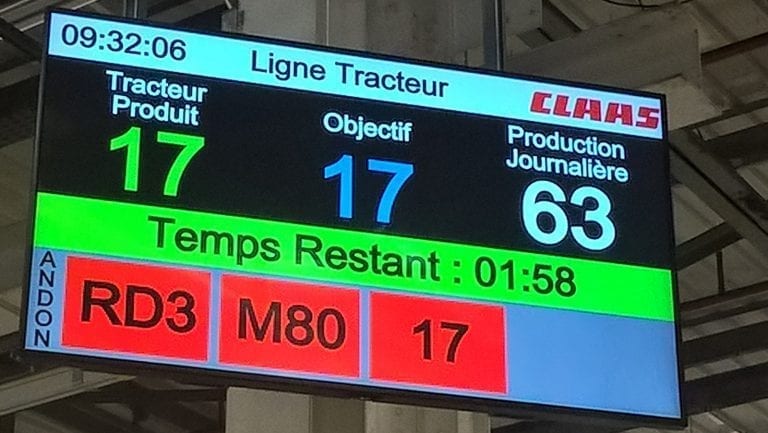
Le bilan : une qualité augmentée et un ROI atteint trois fois plus vite que prévu
Couplé à un accord d’entreprise qui a eu pour conséquence d’intéresser les collaborateurs à l’arrêt… des arrêts, le nouveau système Andon de CLAAS a donc permis d’augmenter à la fois le niveau de qualité et le degré d’efficacité.
« Nous avions tablé sur un ROI à 18 mois : il en a fallu seulement 6 pour que l’Andon déployé par Pingflow soit rentable»
calcule Fabrice Porteboeuf.
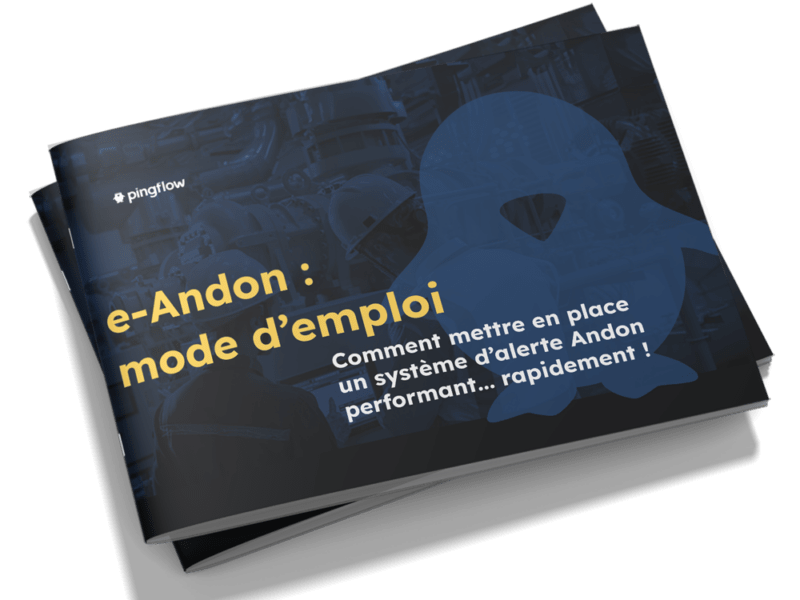
Andon : mode d’emploi
De l’Andon opérateur à l’Andon pilotage en passant par l’Andon flowboard : quels avantages à la mise en place de ces systèmes d’alerte ? Quelles méthodes et pré-requis pour les implanter dans vos unités de production ? Toutes les clés pour réussir votre projet d’Andon digital dans ce guide !