De la production proprement dite aux approvisionnements, l’unité d’assemblage des cabines de paquebots des Chantiers de l’Atlantique a gagné 15 points de productivité en quelques années. Grâce à un projet d’alerte andon et de pilotage digital mené tambour battant.
Des lignes de production actives plus de 90% du temps, un takt-time en constante diminution, moins d’heures supplémentaires… et un climat toujours plus apaisé : aux Chantiers de l’Atlantique, les résultats des efforts entrepris en matière d’excellence opérationnelle sont spectaculaires.
L’explication ? Une démarche d’amélioration continue qui a permis d’anticiper les aléas et de les résoudre (beaucoup) plus vite, tout au long de la chaîne de production.
Les Chantiers de l’Atlantique, berceau des géants des mers
Normandie, France, Queen Mary 2, Harmony of the Seas… C’est à Saint-Nazaire, dans les ateliers des Chantiers de l’Atlantique, que ces célèbres géants des mers ont été assemblés. Depuis 1862, l’entreprise est devenue une référence de la construction de paquebots, mais aussi de navires militaires et plus récemment d’éoliennes offshore. Autant de marchés sur lesquels la demande est très soutenue, et où donc la production est constamment sous tension.
L’unité de production de cabines : 5 lignes taktées et cadencées
À une dizaine de kilomètres du site principal, une plus petite unité (26 000 mètres carrés et 350 opérateurs, tout de même…) s’est spécialisée dans la préfabrication des cabines, qui sont ensuite embarquées et finies à bord des paquebots.
Dans cet atelier, 5 lignes de production, taktées et cadencées, permettent d’assembler les divers modèles de cabines (équipage, standard, famille, pour les personnes à mobilité réduite…) et leurs blocs sanitaires, à raison de 2000 à 2500 cabines par navire en moyenne. Chaque paquebot occupe cette unité de production sur une durée de 4 à 6 mois.
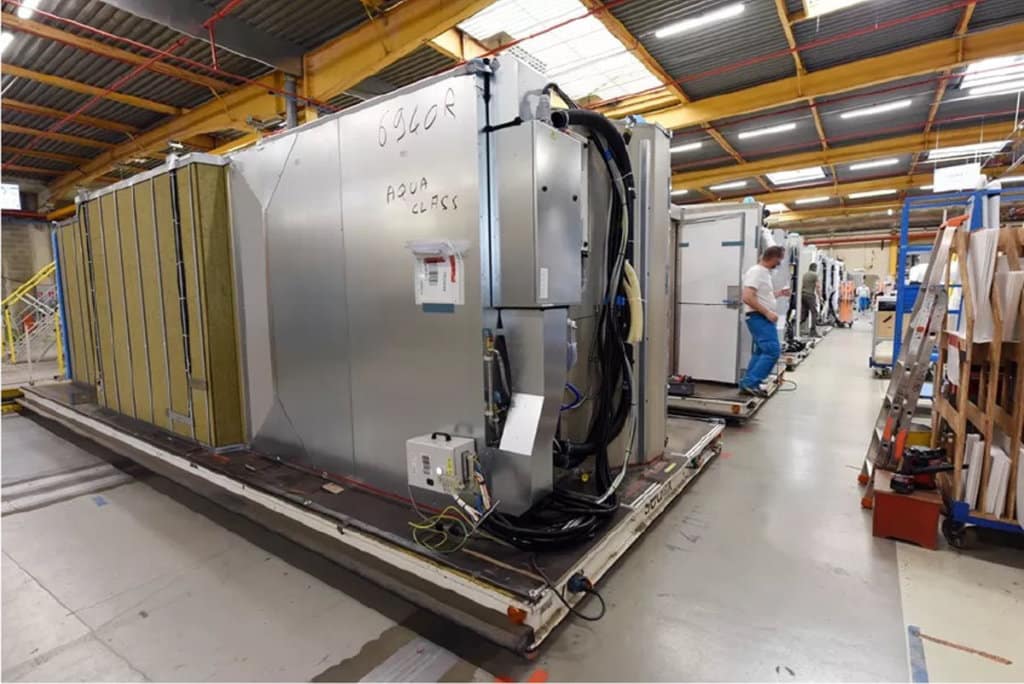
Sur les lignes, objectif lean !
“Le premier constat que l’on peut faire, explique Aurélien Caillaud, c’est que nos lignes n’ont pas d’en-cours : nous sommes en permanence en flux tirés. Conséquence : le moindre aléas sur un des 20 postes de chaque ligne va occasionner un arrêt, et bloquer les 70 opérateurs qui y travaillent”.
Pour résoudre un aléas dès qu’il survient, les Chantiers de l’Atlantique ont mis en place des équipes :
- de “voltigeurs” (côté production), des opérateurs que les chefs d’équipe ou les animateurs de ligne vont envoyer en renfort sur les postes en tension,
- de réapprovisionneurs rapides côté logistique, chargés de fournir les pièces de rechange sur les postes qui en font la demande.
Mais à elle seule, cette organisation ne suffit pas. Depuis quelques années, Aurélien Caillaud, ingénieur lean aux chantiers de l’Atlantique, et son prédécesseur François Robic avant lui, ont donc sollicité Pingflow pour mettre en place des outils permettent d’adopter efficacement des méthodes issues du lean management (Andon et Yo-I-Don) pour piloter et optimiser les lignes d’assemblage cabines. Les objectifs ?
- Obtenir une vision globale précise, et en temps réel, de l’état de chaque ligne de production :
- Identifier au plus tôt les postes en tension et apporter la solution la plus efficiente dans les délais ;
- Synchroniser les postes et cadencer les lignes, afin que chacun commence et finisse ses tâches aux mêmes moments ;
- Fluidifier enfin la communication intra-équipes, mais aussi celle entre la partie production et la partie logistique.
Un chantier mené en 2 phases : d’abord sur les lignes de production, ensuite sur l’approvisionnement logistique.
2019-2020 : cap sur l’andon de production
Le constat de départ : des arrêts de lignes nombreux et coûteux
Dans le cadre d’une production en flux tirés, des aléas, il y en a toujours : avant d’entamer sa collaboration avec Pingflow, l’atelier des cabines subissait une heure d’arrêt en moyenne par jour.
À ces incidents s’ajoutait la problématique des changements de ligne (un nouveau type de cabine qui entrait en production). Entre deux “batch”, le temps d’arrêt et de redémarrage de la ligne était aussi d’une heure. Mis bout à bout, ces retards pouvaient impacter fortement la cadence de production, et donc la livraison du paquebot en bout de chaîne.
La réponse de Pingflow : l’alerte andon digital depuis les postes opérateurs
Fort logiquement, les équipes des Chantiers de l’Atlantique ont donc d’abord souhaité s’attaquer au sujet des arrêts de ligne liés à des incidents de production à proprement parler.
Avec le concours de Pingflow, chaque poste de travail a été équipé d’une tablette qui permet à l’opérateur de remonter d’un clic des informations telles que :
- sa fin de travail,
- un incident bloquant,
- ou non bloquant.
Ces incidents sont immédiatement transmis par SMS et email aux chefs d’équipe, et affichés sur les moniteurs de grande taille implantés à des endroits stratégiques de l’atelier pour y diffuser les informations en temps réel sur l’état de l’activité. Les interventions et renforts nécessaires pour résoudre l’incident et faire repartir la production arrivent plus vite, et l’ensemble de l’activité de la ligne est suivi plus finement.
En back-office, tout le système est connecté à l’ERP afin de fournir le “film” de production prévisionnel de la journée et à une interface web qui permet :
- en amont, de paramétrer les horaires de travail, les profils et coordonnées des utilisateurs,
- en aval, de visualiser les incidents sous la forme de journaux et de graphiques et d’en tirer un historique pour l’analyse qualité.
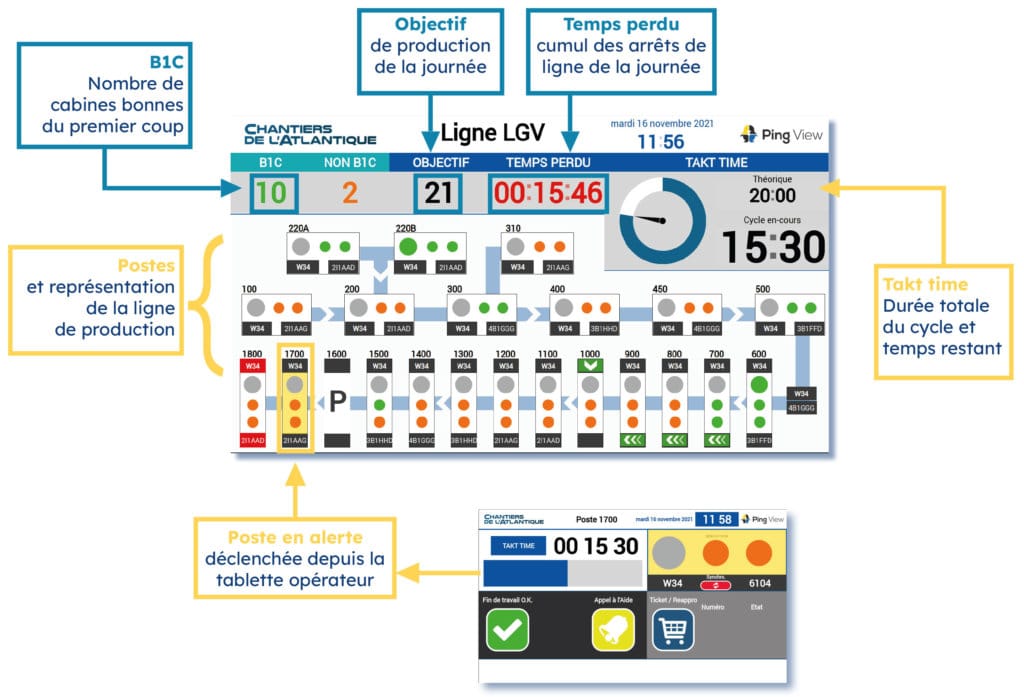
Des premiers résultats spectaculaires
Déployé en 2019, cette première “brique” d’andon a permis à l’atelier cabines d’enregistrer des résultats plus que probants :
- Des temps d’arrêts divisé par 3… et plus : d’une heure par jour, l’atelier est passé à 20, puis 10 minutes/jour ;
- Des lignes toujours plus efficaces : de 80% du temps ouvré, l’unité de production est passé à 90-95% ;
- Une nette baisse des heures supplémentaires (souvent nécessaires pour “boucler” la production de la semaine), de l’ordre de 10%.
Pari gagné ? Sauf que les Chantiers de l’Atlantique ne comptaient pas s’arrêter en si bon chemin…
À LIRE AUSSI > Système andon : comment CLAAS digitalise la gestion des incidents
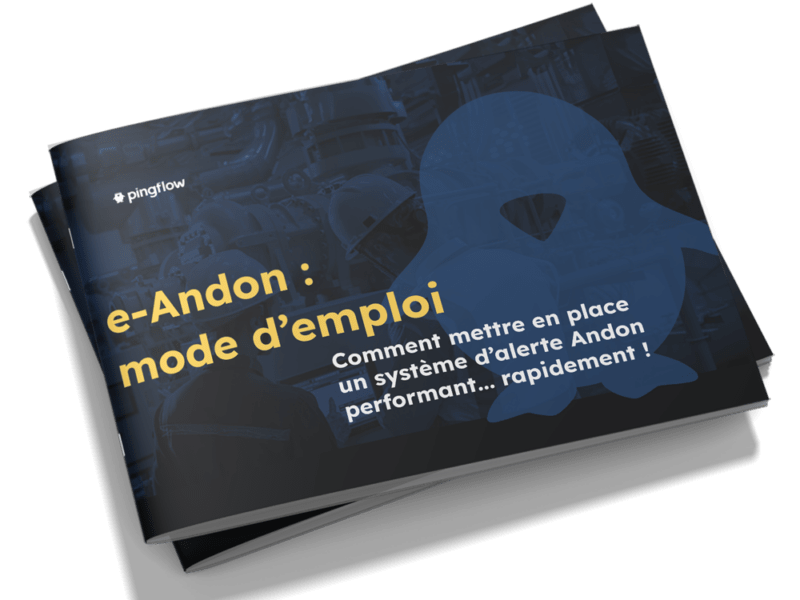
eBook : e-Andon, mode d’emploi
Votre guide pour mettre en place un système d’alerte Andon performant… rapidement !
2021 : un cran plus loin avec l’andon logistique
Car après avoir fluidifié la résolution des incidents de production, les équipes se sont aperçues que 80% des arrêts de lignes résiduels étaient liés à des pièces non-conformes : éléments du bloc sanitaire abîmés, pièces dégradées, etc.
Historiquement, un opérateur confronté à une pièce défectueuse devait remplir à la main une fiche de non-conformité, et la transmettre aux équipes de réapprovisionneurs rapides pour qu’ils aillent récupérer la pièce de rechange en stock, l’acheminer vers le poste en question, et clôturer ce “ticket”. Un processus lourd, chronophage… et donc éminemment optimisable !
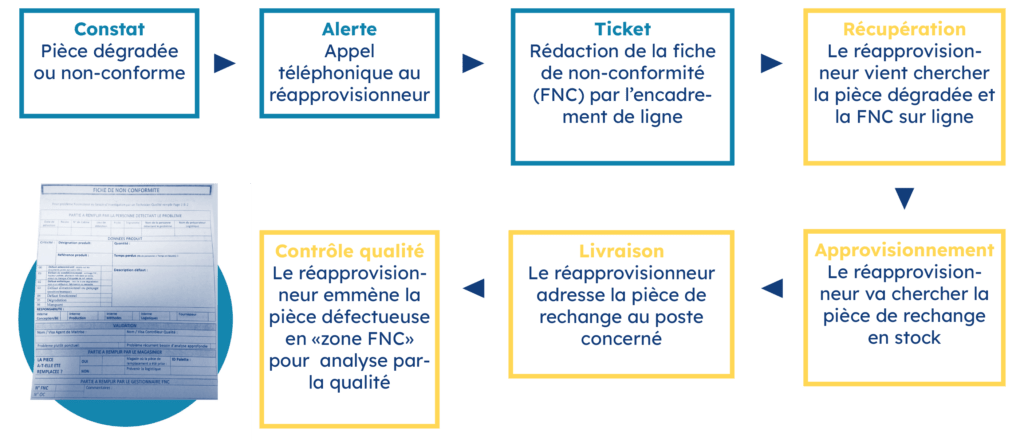
D’autant plus qu’il générait de fortes tensions entre les équipes production et logistique, “qui se renvoyaient la balle lors de ce type d’incidents, observe Aurélien Caillaud. Or l’un des bénéfices non-quantifiables mais bien réels de de la mise en place de l’andon de production avec Pingflow, c’était justement un net gain de sérénité dans l’atelier : les opérateurs savent désormais que l’incident qu’ils ont déclaré est bien identifié et en cours de résolution. Nous avons voulu que nos équipes de réapprovisionneurs, qui sont par nature soumises à l’urgence et au stress, bénéficient elles aussi de conditions de travail plus apaisées”.
Un nouveau processus co-conçu avec les équipes concernées
Pour dénouer ce problème, Aurélien Caillaud a d’abord écouté le “terrain”, et recueilli les irritants des équipes…
- … production : fiches trop longues à remplir, réapprovisionneur injoignables, réapprovisionnement trop lent, occasionnant des arrêtes de ligne ;
- … logistique : fiches mal remplies ou illisibles, trop de temps au téléphone, impossible d’organiser et de se concentrer sur sa tournée ;
- … qualité : déclarations des non-conformités intraçable set inexploitables.
Pas simple, surtout dans le contexte de ces ateliers :
- très vaste (26 000 m2), donc avec des tournées longues
- avec de nombreuses références (3000 par cabine), donc des réapprovisionnements complexes
- de plus en plus cadencés, avec un takt time divisé par 1,5 ces 5 dernières années (il est passé de 30 à 19-20 minutes en moyenne)
Du 100% papier au 100% digitalisé : un andon logistique 100% efficient
C’est grâce à cette phase d’écoute terrain qu’Aurélien Caillaud a pu déployer avec Pingflow un système andon logistique adapté aux besoins de ses “clients” internes des trois pôles production, logistique et qualité, dont il vous fait lui-même la démonstration
Retrouvez le témoignage intégral d’Aurélien Caillaud sur la collaboration de Pingflow et des Chantiers de l’Atlantique dans notre webinaire en replay
Vélocité, productivité, sérénité : des indicateurs au vert !
En digitalisant tout ce processus d’alerte, et en éliminant la paperasse et les irritants du parcours des réapprovisionneurs, les Chantiers de l’Atlantique ont à nouveau observé d’énormes gains de productivité :
- Sur la vélocité des opérations, avec un délai de réapprovisionnement réduit de plus de moitié : de 33 mn avant, on en est aujourd’hui à 12-13 minutes en moyenne ;
- Sur la sécurisation du takt time : ces délais de réapprovisionnement express laissent une marge sur le cycle actuel, déjà en nette baisse ;
- Sur l’efficacité des lignes au global : de 700 minutes de temps d’arrêt par mois, l’atelier est passé à 200-250 minutes ;
- Sur le suivi de la qualité, les équipes disposent désormais d’un vrai tableau de bord permettant d’identifier et de mesurer les dérives par fournisseur, par pièce… et donc de prendre les mesures adéquates ;
- Sur la sérénité des opérateurs logistiques, désormais beaucoup plus en contrôle de leur temps et de leur tournée.
e-Andon : le premier vers l’usine 4.0
Découvrez les principes de fonctionnement de l’Andon, ses dernières innovations, les types d’opérations industrielles qu’il optimise, ainsi que son ROI pouvant atteindre +15 % de TRS et ses bénéfices concrets en production.
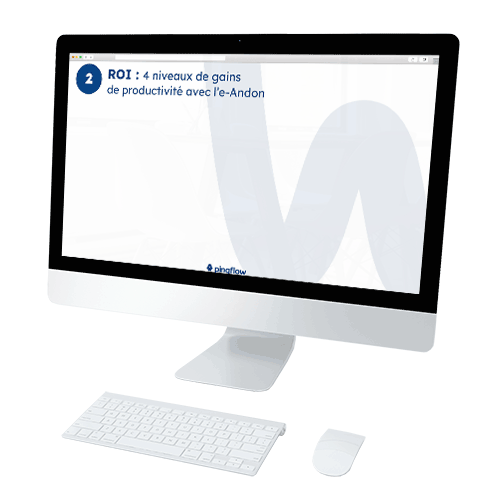
Dans les tuyaux : des innovations qui se diffusent sur toute la chaîne de production
Engagés dans une démarche d’amélioration continue, les Chantiers de l’Atlantique vont maintenant capitaliser sur les démarches entreprises lors des 2 premières phases du projet, pour pousser encore plus loin le pilotage de l’activité, avec :
- un andon “picking”, afin d’optimiser la logistique au-delà des réapprovisionnements d’urgence, notamment pour le train qui approvisionne les lignes depuis les stocks
- une information en temps réel de l’état de la production à destination de la logistique, afin de redonner de la visibilité à cette dernière.
Les facteurs-clés de succès du projet des Chantiers de l’Atlantique
Les remarquables résultats observés par l’unité d’assemblage cabines ne sont ni miraculeux, ni le fruit du hasard. Mais avant tout la conséquence d’un projet bien mené autour de 3 facteurs-clés :
- Une avancée priorisée par “lots” : plutôt qu’un “méga-projet” global (mais qui n’aurait peut-être jamais vu le jour), les Chantiers de l’Atlantique ont procédé par étapes. D’abord le problème le plus urgent (les arrêts de ligne côté production), puis après ce premier succès la priorité numéro 2 (les réapprovisionnements), enfin une généralisation plus poussée ;
- Une courbe d’apprentissage respectée : les équipes ont pris le temps d’observer les premiers résultats, de lister les points d’amélioration, avant d’itérer ;
- L’écoute terrain en vertu cardinale : l’utilisateur est roi, et tous les outils et interfaces ont été conçus pour répondre le plus simplement possible aux besoins exprimés.
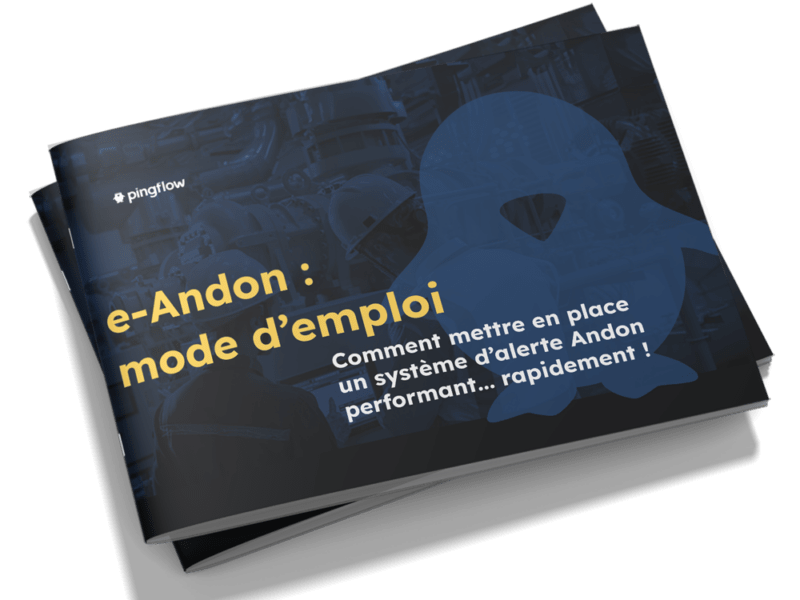
eBook : e-Andon, mode d’emploi
Votre guide pour mettre en place un système d’alerte Andon performant… rapidement !