En à peine 3 mois, les équipes du site du groupe Atlantic à Billy-Berclau ont réussi à digitaliser leurs supports de management visuel d’AIC (TOP 5, TOP 30…). Des supports totalement interconnectés à leurs autres solutions de pilotage de l’usine, avec une totale autonomie dans le déploiement et l’amélioration continue de leurs supports. Comment ? Explications.
Dans l’usine du groupe Atlantic de Billy-Berclau (62), on n’a pas de temps à perdre ! Démarrée en 2016 avec 50 personnes, l’usine dédiée essentiellement à la production de pompes à chaleur en emploie aujourd’hui 500, “sort” plus de 200 000 produits par an et prévoit d’accélérer encore jusqu’à 350 000 dans les 2 ans qui viennent.
Un démarrage plein gaz qui caractérise aussi la façon dont ses équipes ont digitalisé leurs AIC (Animations à Intervalle Court, une quinzaine de rituels différents dans cette usine) en à peine 3 mois ! Le tout sans jamais confondre vitesse et précipitation…
Leur recette ?
- des objectifs limpides dès le départ (ce qui facilite la recherche du bon partenaire et le cadrage du projet)
- le métier et la DSI qui travaillent main dans la main
- un temps d’avance en permanence sur la suite du projet : la façon dont les équipes vont prendre en main l’outil, et comment ce dernier va pouvoir être décliné à grande échelle après les premiers tests…
POUR EN SAVOIR PLUS > Qu’est-ce qu’une animation à intervalle court (AIC) ?
Un objectif clair : rendre les AIC plus efficients
Des rituels déjà bien structurés…
“Les AIC, c’est quelque chose qui est très ancré dans l’usine, et dans tout le groupe Atlantic depuis des années, explique François Huyge, le responsable de production de l’usine de Billy-Berclau. TOP 5, pour les points de démarrage de chaque shift pour chacune de nos 14 lignes de production, TOP 30 (la réunion de coordination de production) et un rituel qu’on appelle InterGAP (pour Groupes Autonomes de Production) qui permet aux animateurs de ligne de faire un point sur leurs priorités et besoins… On est friands de ces rituels”.
Les AIC chez Atlantic Billy-Berclau : 46 rituels par jour
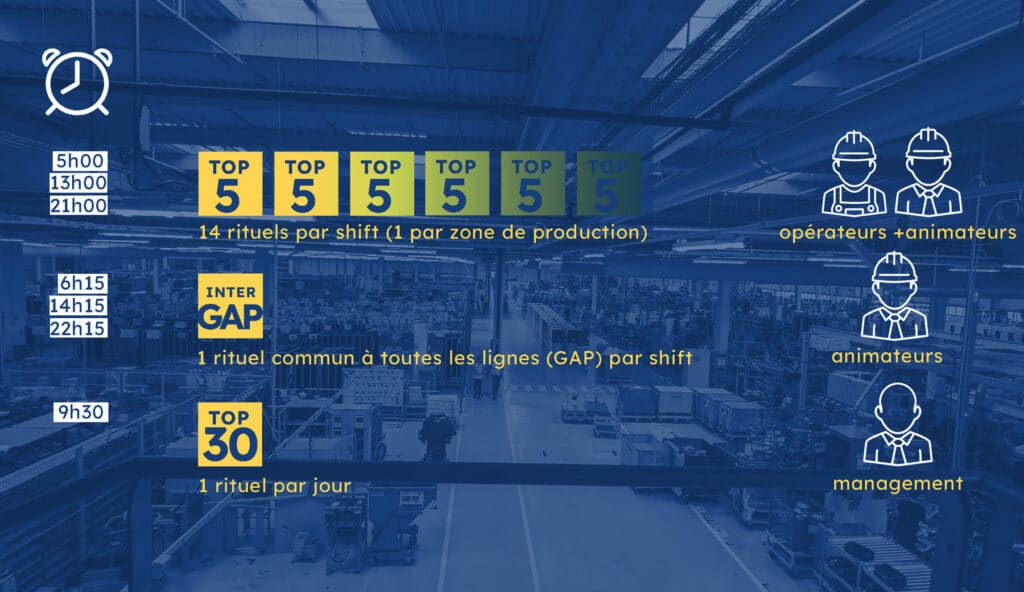
… mais un temps de préparation des rituels à optimiser
Avant de se tourner vers Pingflow, les équipes d’Atlantic à Billy-Berclau organisaient leurs AIC de façon traditionnelle : tableaux blancs, impressions papier, cartelettes pour les actions à mener, présentations Powerpoint…
Le problème ? Ce système, efficace et bien rôdé, mais “les opérateurs passaient leur temps à recopier des informations des tableaux blancs vers les fichiers informatiques, et vice-versa, avec tous les risques de perte d’information et d’erreurs que cela suppose en prime”, déplore François Huyge. Et avec plus de 40 rituels quotidiens à organiser, le compteur temps grimpe très vite…
Des critères de choix clairs
Partant de ce constat, François Huyge s’est donc mis en quête d’une solution lui permettant de digitaliser les AIC de son usine. Avec des attentes très claires :
- un système qui simplifie et fluidifie la récupération des informations sur la production, et leur “traduction” visuelle en indicateurs clairs,
- une solution qui permette de centraliser et de suivre les différents plans d’action de l’usine et de chaque ligne
- une solution qui s’intègre aisément enfin dans le système d’information du site.
“Chez Atlantic, on aime bien avoir la main sur nos outils : je cherchais donc une solution intuitive, qui nous permette d’être rapidement autonomes, et surtout modulable parce qu’on fait les choses à notre façon, énumère le responsable de production. J’ai étudié plusieurs solutions du marché : seul Pingflow cochait toutes les cases. Les autres solutions étaient soit inadaptées à notre besoin, soit beaucoup trop formatées”.
Après des premiers échanges au printemps 2022, Atlantic Billy-Berclau se lance donc dans son projet de management visuel digital avec Pingflow.
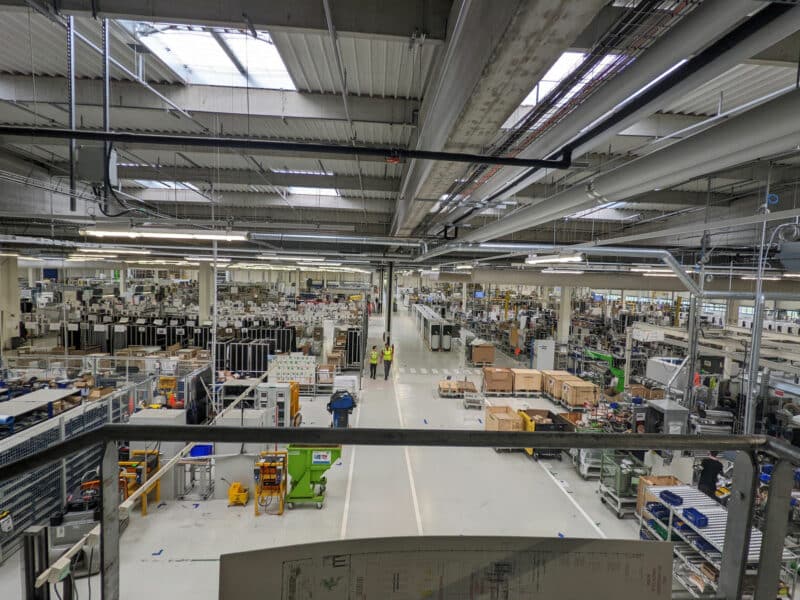
L’IT : un rôle moteur dans l’interconnexion aux systèmes et à la data du site
Dans un projet aussi structurant sur la bonne marche de la production, l’implication des équipes IT est évidemment la condition sine qua non d’un bon déploiement. Mais leur rôle va bien au-delà, et commence surtout bien avant la phase de mise en production : c’est dès le cadrage du projet qu’ils ont un rôle à jouer.
Coup de chance : à Billy-Berclau, l’équipe informatique industrielle a l’habitude de travailler au plus près du terrain, et on pu apporter leur concours sur deux dimensions essentielles :
- la data : comment la structurer et si besoin la créer pour l’exploiter au mieux dans le cadre des AIC
- la connectivité : comment interconnecter Pingflow avec le “stack” d’outils existants dans l’usine, et en tirer le meilleur parti.
À LIRE AUSSI > 6 étapes pour mettre en place le management visuel digital
Le rôle des outils : lequel fait quoi (et comment s’intègre Pingflow)
Chez Atlantic, 2 logiciels internes servent principalement au pilotage de la production :
- Suprat, orienté sur le suivi de la qualité
- Ocean, qui collecte des données machine ou sur les lignes pour traiter la performance
Soucieux de ne pas “empiler” les briques logicielles, les équipes IT d’Atlantic ont donc commencé par un exercice de réflexion : “en interne, nous avons redéfini le rôle de nos différents outils, explique Nicolas Denis, chef de projet informatique industrielle. L’idée, c’est que ces outils se complètent, et qu’on ne leur attribue pas des fonctions pour lesquelles ils ne sont pas faits.
Conclusion de cette réflexion ?
“On réserve Pingflow à des enjeux d’animation : même si ce serait techniquement possible, on n’y fait pas de traitement de données
poursuit Nicolas Denis.
La maîtrise des données : une base saine pour démarrer
Autre enjeu pour lequel l’implication de l’IT a été déterminante : les données. “C’est un sujet qu’on maîtrise très bien : comment nos données sont formées, structurées… constate Nicolas Denis. Ça a donc été plus simple en amont de se poser les bonnes questions pour qu’elles soient facilement exploitables dans Pingflow, et surtout toujours structurées de la même façon”.
Résultat : lorsqu’il a fallu concevoir les wallboards (les affichages utilisés lors des différents AIC), la base était “propre”, cohérente… et facilement déployable sur l’ensemble des lignes pour couvrir le site en quelques jours à peine.
Le guide ultime des rituels d’équipe pour animer la performance
Mettre en place les AIC : quelle méthodologie ? Comment les digitaliser ? Votre plan d’action, étape par étape, est à retrouver dans nos eBook
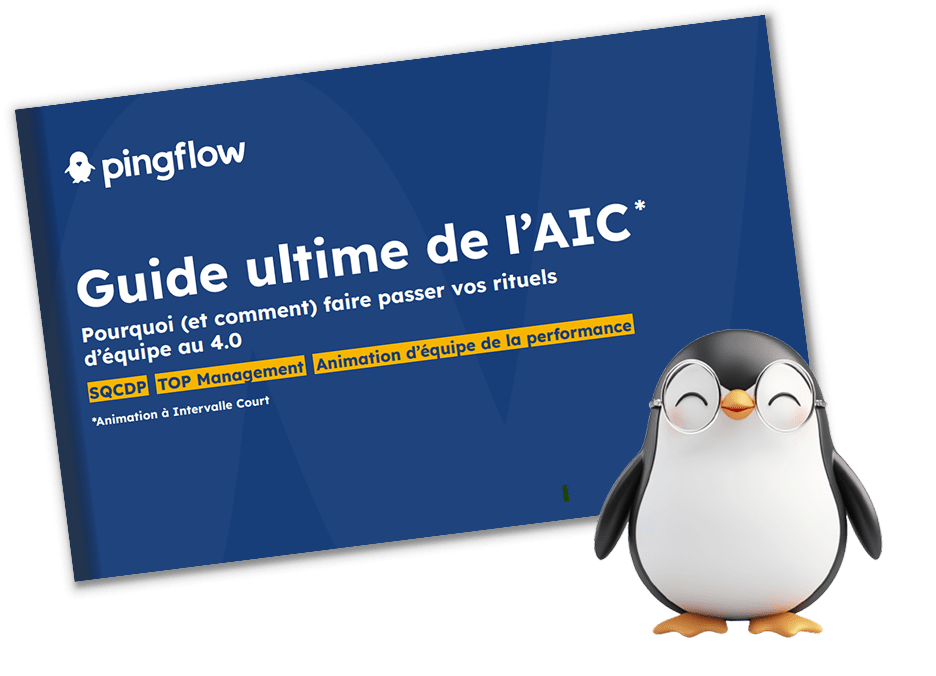
Une prise en main facilitée
Car les différents wallboards ont été “templatisés”(même structure globale, même format des indicateurs) au maximum : d’une ligne à une autre, les wallboards des TOP 5 sont structurés de la même manière, et seules les informations changent. “Lorsqu’on doit en déployer un de plus, c’est l’affaire de 5 minutes”, sourit Nicolas Denis. L’optimisation, toujours…
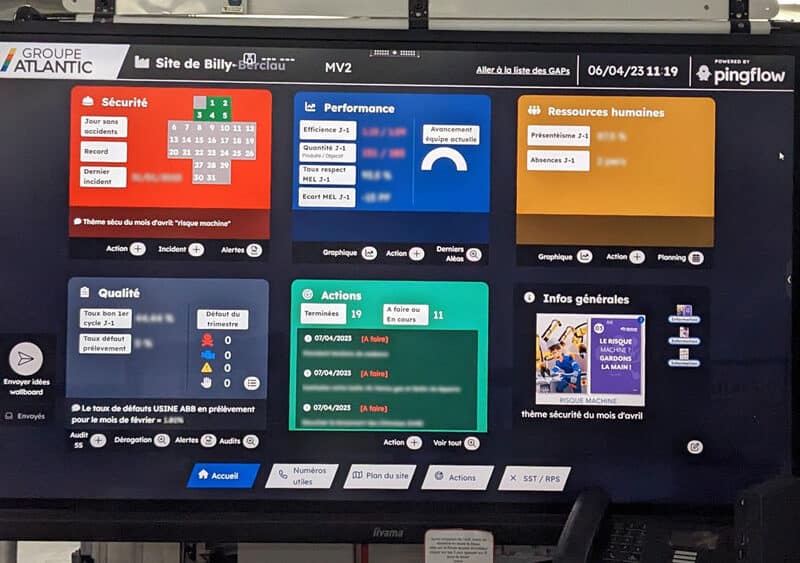
Même design, même hiérarchie des informations, mais données personnalisées dans 2 wallboards différents : avec un template unique, les équipes d’Atlantic ont pu déployer leurs wallboards d’AIC très rapidement dans les différentes zones de l’usine.
De la conception à l’animation : une solution intuitive
Dernier facteur qui a permis à Atlantic d’aller si vite dans le déploiement de son projet d’AIC digital : la simplicité d’usage de Pingflow. “Côté conception des wallboards, la solution est très intuitive : aucun besoin d’être informaticien pour y parvenir”, apprécie François Huyge.
Même constat du côté des utilisateurs finaux (animateurs de lignes et opérateurs), qui se sont rapidement approprié Pingflow, et notamment Table, la solution de gestion de bases de données “No Code” intégré dans Pingflow, qui permet notamment de créer des formulaires de saisie interactifs (pour la remontée d’incidents, d’absences, etc.), mais aussi tous les plans d’actions, documentés, triés, priorisés… et à jour.
Digitalisation des AIC : votre checklist avant/après
Faites l’état des lieux de vos rituels actuels, et préparez votre dispositif d’animation de la performance de demain : indicateurs, déroulé, process de résolution de problèmes…
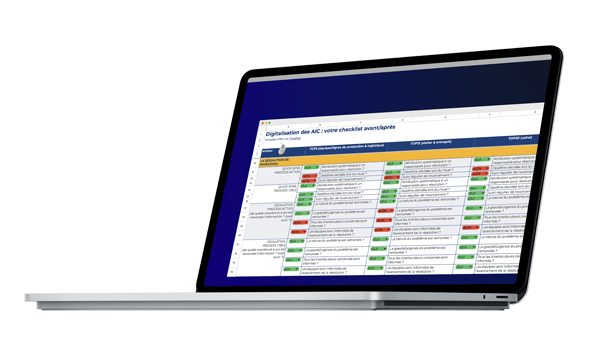
Les résultats : des AIC moins chronophages, plus interactifs, et plus impactants
Quelques mois après ce déploiement éclair, les équipes d’Atlantic identifiant déjà un triple gain :
- de temps, dans la préparation des AIC
- d’efficience de ces rituels, avec des équipes plus concentrées
- d’impact, avec des plans d’actions mieux suivis, et une meilleure visibilité sur l’activité
Pour le premier, qui était l’objectif principal de François Huyge au départ, le constat est clair : 80% de ce que les animateurs devaient resaisir avant la réunion est désormais à disposition automatiquement dans le wallboard. “Clairement, la demi-heure par AIC passée à aller chercher et recopier des informations a quasiment disparu”, se félicite le responsable de production.
Pour le second, François Huyge observe que le fait d’avoir un support unique (l’écran qui diffuse le wallboard) et un support interactif, rend les rituels plus participatifs et les équipes “plus attentives et plus dans la discussion”.
Pour le troisième, la digitalisation des plans d’action constitue un gros plus. Et au-delà, son objectif d’avoir un aperçu plus synthétique et plus précis du “pouls de l’usine” (primordial notamment lors des TOP 30) est largement rempli.
Management visuel digital : calculez le ROI de votre projet
Bien mesurer l’investissement nécessaire, évaluer au plus juste des gains en retour : quel sera le retour sur investissement de votre projet de management visuel digital ? Avec ce simulateur de ROI, vous aurez la réponse… et une réponse basée sur vos indicateurs.
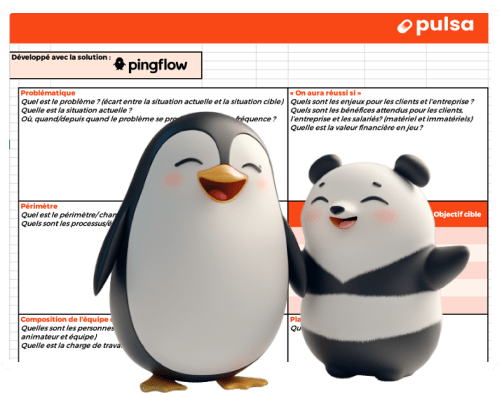