Dans l’industrie, l’Andon est une méthode lean qui permet de répondre plus rapidement et plus efficacement aux incidents de production. Les différents types d’Andon, les grands principes, les gains de productivité à en attendre, des exemples… On vous explique tout.
Comme de nombreux concepts et méthodes lean, l’Andon a été popularisé dans le cadre du Toyota Production System au siècle dernier. L’idée ? Permettre de détecter, signaler, et résoudre des problèmes liés à la production plus rapidement et plus efficacement.
Les principes de fonctionnement de l’Andon
L’Andon est donc essentiellement un système d’alertes visuelles et/ou sonores :
- un opérateur, un contrôleur qualité, ou même une machine selon le type d’Andon qui est mis en place signale un problème,
- un leader ou un membre d’un service support, informé du problème, intervient pour le régler.
L’Andon digital : un système d’alerte plus efficace et plus flexible
Traditionnellement, cette alerte était signalée grâce à un système lumineux (d’où le terme japonais d’Andon, qu’on traduit par “lumière vers laquelle il faut aller”) et parfois des alertes sonores. Il prenait le plus souvent la forme de colonnes lumineuses disposées sur les postes de travail.
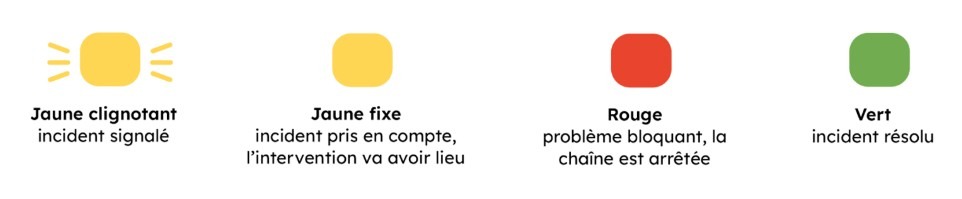
Grâce aux nouvelles technologies, l’Andon digital (ou e-Andon) permet :
- de prévenir plus efficacement leaders et services supports : les grands écrans disposés dans les ateliers, les alertes par e-mail et par SMS assurent d’alerter le responsable compétent plus vite et plus directement, notamment lorsqu’il n’est pas physiquement présent dans l’atelier (en réunion, par exemple),
- d’adapter plus facilement la disposition des “alerteurs” lorsque le plan de production change : une télécommande radio ou une tablette opérateur se déplacent plus aisément que les cordes et colonnes lumineuses d’antan,
- de passer plus simplement en démarche d’amélioration continue : les incidents sont “codés” informatiquement, et donc renseignés dans une base de données qui va permettre de les analyser efficacement pour lancer des plans d’actions correctifs.
L’Andon digital, parce qu’il permet la circulation et l’affichage des informations en temps réel, est donc l’un des ingrédients du juste à temps.
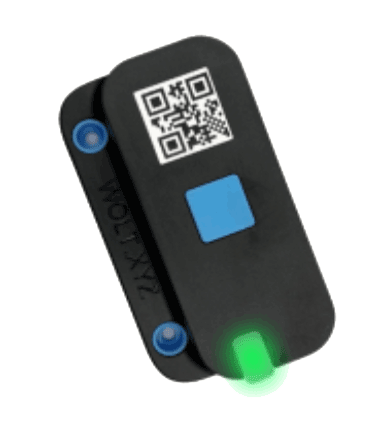
Télécommande radio pour les alertes simples
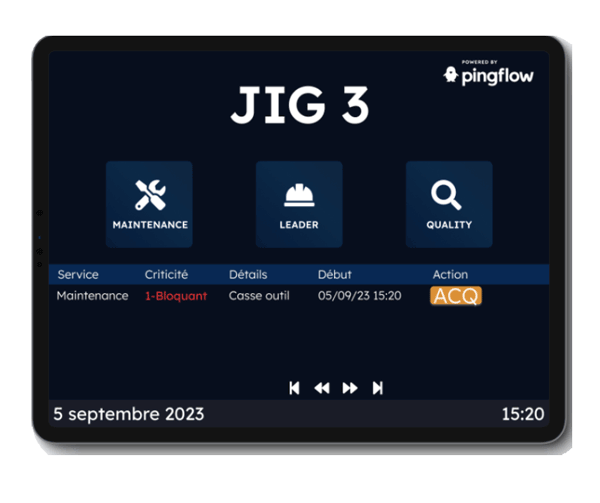
Tablette pour codifier les appels et saisir des informations : à chaque problématique sa réponse.
À LIRE AUSSI > Système andon : comment CLAAS digitalise la gestion d’incidents
Quelles sont les phases de déroulement de l’Andon ?
Un processus Andon classique se décompose en 4 phases :
- Détection : soit humaine (Andon opérateur, Andon approvisionnement), soit automatique (Andon machine), c’est le moment du déclenchement de l’alerte Andon
- Traitement : à cette phase, l’incident est qualifié selon sa gravité, et affecté à qui de droit (le manager en charge, l’équipe maintenance…)
- Visibilité : ici s’opèrent les règles de communication de l’alerte, en direct vers les responsables (SMS, e-mail) et/ou collective (affichage dans l’atelier)
- Amélioration : lorsque l’incident est résolu, on le renseigne dans une base de données qui servira aux équipes chargées de résoudre proactivement les incidents les plus fréquents ou les plus bloquants à l’avenir.
DÉTECTION | TRAITEMENT | VISIBILITÉ | AMÉLIORATION |
![]() | ![]() | ![]() | ![]() |
Détecter vos anomalies dès qu’elles surviennent | Prioriser Critique > Urgent > Bloquant > Gênant… Affecter Par e-mail, SMS, affichage… Escalader Selon urgence, disponibilité : niveau 1 > 2 > 3 | Niveau individuel Manager (SMS/e-mail) Opérateur (pupitre, tablette, visio) Niveau équipe Écrans, colonnes lumineuses, avertisseurs sonores | Historisation et traçabilité Durée Pareto Fréquence Actions etc. Amélioration continue |
Quelles sont les principales fonctionnalités d’un système e-Andon ?
Pour donner sa pleine mesure, un système Andon digital doit comporter :
- des appareils d’appel Andon, déclenchés par les opérateurs (boutons, tablettes…) ou par automatisme (un dépassement de seuil ou un indicateur incohérent entraînant l’alerte),
- un processus d’escalation, pour prévenir le premier superviseur à prévenir, éventuellement le relancer sans réponse de sa part, puis passer au niveau supérieur…,
- des fonctionnalités “hors alertes” mais essentielles pour le suivi : affichage du takt time et des indicateurs de production (objectif, réalisé, écart) pour passer d’un simple système de détection/résolution de problèmes à une aide au pilotage d’une unité de production (via par exemple un flowboard),
- et enfin des fonctionnalités de collecte et d’analyse de données, pour mesurer la fréquence des incidents par cause, type, zone, gravité… et travailler à les réduire par l’amélioration continue.
Quels sont les différents types d’Andon ?
On distingue deux grandes typologies d’Andon :
- les Andons “simples”, qui s’attachent à détecter et résoudre des problèmes localisés sur les lignes de production,
- les Andons “avancés”, qui souvent combinent plusieurs types d’Andon simples ou associent Andon pour la partie alerte et systèmes de management visuel de la production (flowboard) ou d’animation des équipes (AIC).
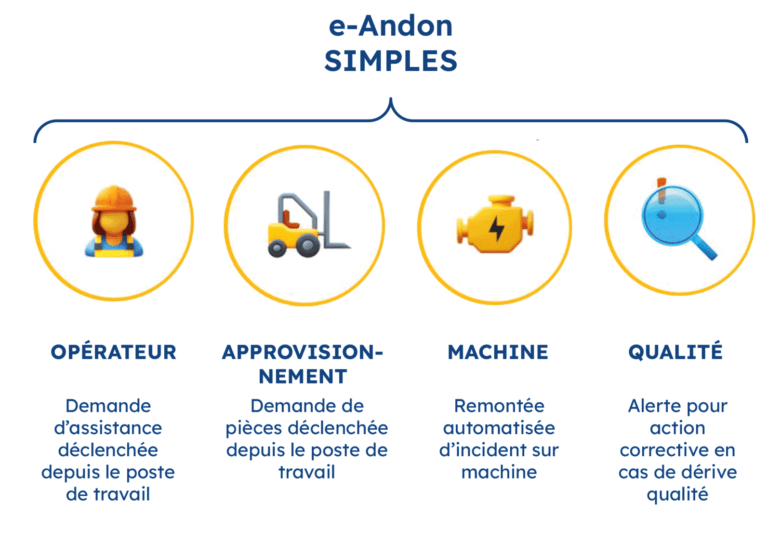
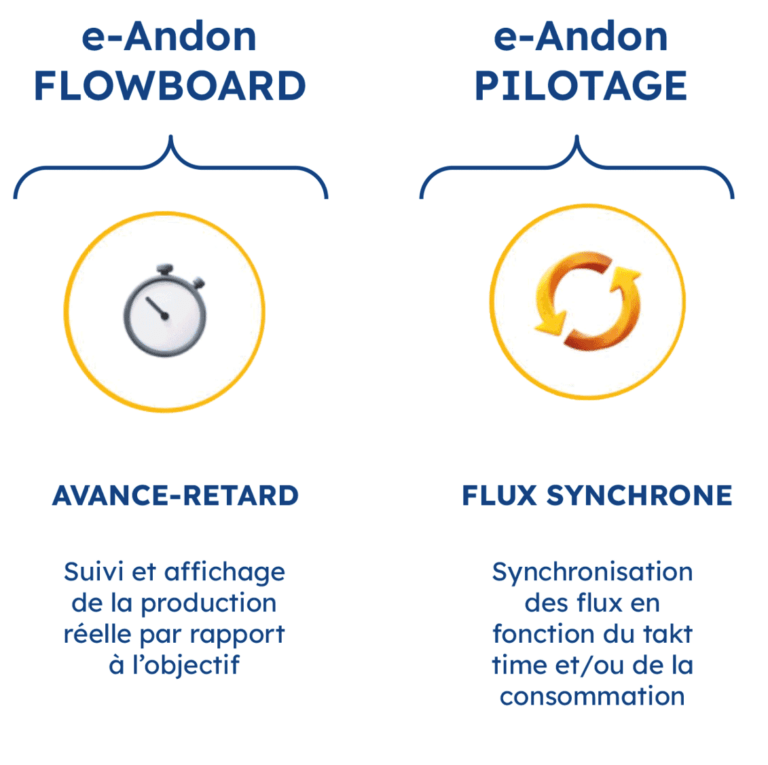
À LIRE AUSSI > Quels sont les différents types d’Andon et comment les mettre en place ?
Votre guide pour mettre en place un système d’alerte Andon performant… rapidement !
Votre guide pour mettre en place un système d’alerte Andon performant… rapidement !
Quels sont les avantages de la mise en place de l’Andon ?
Pourquoi décide-t-on généralement de mettre en place un système Andon ? C’est généralement pour une (ou plusieurs) de ces 4 raisons :
- Une organisation rigide : manque de réactivité, suivi de la qualité pas assez proactif,
- Une organisation opaque : les anomalies comme les indicateurs de production ne sont pas assez visibles, ce qui complique la prise de décision, et oblige à surconsommer les ressources support,
- Un suivi défaillant : le management est en mode “pompier” permanent pour assurer le respect des cadences,
- Une traçabilité insuffisante : les incidents ne sont pas documentés, empêchant toute démarche d’amélioration continue.
Réactivité : des incidents résolus 2 fois plus vite
Le premier bénéfice de la mise en place d’un système Andon, c’est l’accélération de la résolution des incidents. On gagne en effet du temps à toutes les étapes du processus :
- l’alerte est lancée plus vite, car chaque poste ou machine est équipé d’un dispositif d’appel, avec des critères clairs,
- l’incident est pris en compte plus vite par le leader ou le service support, grâce à la multiplication des moyens de contact (SMS, email, affichage digital dans l’atelier et les bureaux),
- l’indisponibilité du premier “contact” dans le processus d’alerte Andon est rapidement contrebalancée par l’escalation.
Résultat ? On constate chez nos clients un temps de résolution des incidents divisé par 2 en moyenne, et des temps d’arrêt de lignes en très nette baisse.
CAS CLIENT > CLAAS : 30 secondes gagnées par appel grâce à l’e-Andon
Visibilité : des équipes mieux informées, plus autonomes, et des prises de décision plus efficaces
Grâce à l’e-andon, chaque acteur est tenu informé en temps réel :
- l’opérateur concerné sait précisément si son appel a été pris en compte, et si la résolution est en cours,
- ses collègues sur la même ligne de production connaissent la nature de l’incident, s’il est bloquant,
- son leader, la maintenance, le contrôle qualité, la logistique interne… sont alertés, et savent qui est affecté à la résolution de l’incident.
Chacun peut donc prendre les bonnes décisions à l’instant T, avec la certitude de disposer des bonnes informations. Les bienfaits ? Ils sont à la fois humains et organisationnels :
- moins de stress, et d’équipes qui se renvoient la balle en cas d’incident,
- une vraie cohésion autour d’objectifs et d’indicateurs clairs,
- une vraie optimisation des ressources humaines, notamment côté management et services support.
CAS CLIENT > TIAG Industries : 5 à 8% de temps gagné pour les managers d’ateliers
Excellence opérationnelle : un TRS en hausse de +5 à +15%
Conséquence logique des 2 points précédents : l’Andon digital améliore considérablement la productivité d’une unité de production, en :
- fiabilisant la supply chain (moins de surstock, moins de ruptures d’approvisionnement),
- minimisant le coût de la non-qualité,
- accélérant les opérations sur la ligne de production et en “collant” mieux au takt time
Quel gain de productivité, au juste ? Sur le terrain, nous mesurons une augmentation du TRS (Taux de rendement synthétique) chez nos clients de 5% (e-Andon “simple”) à 15% (e-Andon “pilotage”).

Très rapides à déployer (moins d’un mois pour une version simple), les systèmes e-Andon offre un ROI quasi-immédiat (visible en moins de 6 mois), et incrémental !
CAS CLIENT > La rentabilité d’un système d’e-Andon “approvisionnement” chez Toyota
CAS CLIENT > Les gains de productivité chez Faiveley grâce à l’e-Andon “opérateur”
Amélioration continue : l’Andon, accélérateur de transformation digitale
Le dernier grand bénéfice de l’Andon digital, c’est l’étendue des possibilités qu’il offre pour améliorer en continu vos opérations. Pourquoi ?
- Il génère quantité de données, incident après incident, permettant à la fois d’avoir une vision beaucoup plus claire de l’état normal, insuffisant ou performant de vos lignes de production, mais aussi des causes récurrentes de problèmes à corriger,
- ces données permettent d’alimenter et de prioriser les plans d’action correctifs qui vont minimiser ou faire disparaître ces problèmes à l’avenir,
- et elles constituent le “socle” de vos futurs projets de transformation digitale : avec un e-Andon opérationnel, vous disposez des informations nécessaires pour déployer le pilotage de la production par la data (flowboard), offrir à vos équipes des écrans de management visuel d’AIC en temps réel, etc.
CAS CLIENT > Aux Chantiers de l’Atlantique, Andon opérateur, Andon logistique, optimisation du pilotage : +15% de TRS en 3 ans